An introduction to Solid State Relays
INTRODUCTION:
Because of its excellent performance, solid state relay has become an essential industrial control device in many fields.
This is an introduction to solid state relays, through this article you will learn What is a solid state relay? What are the types of solid state relays? How do solid state relays work? How to select the solid state relay? How to use solid state relays?
You can quickly navigate to the chapters you are interested in through the Directory below, and the Quick Navigator on the right side of the browser.
CONTENTS
§1. What is a Solid State Relay (SSR)
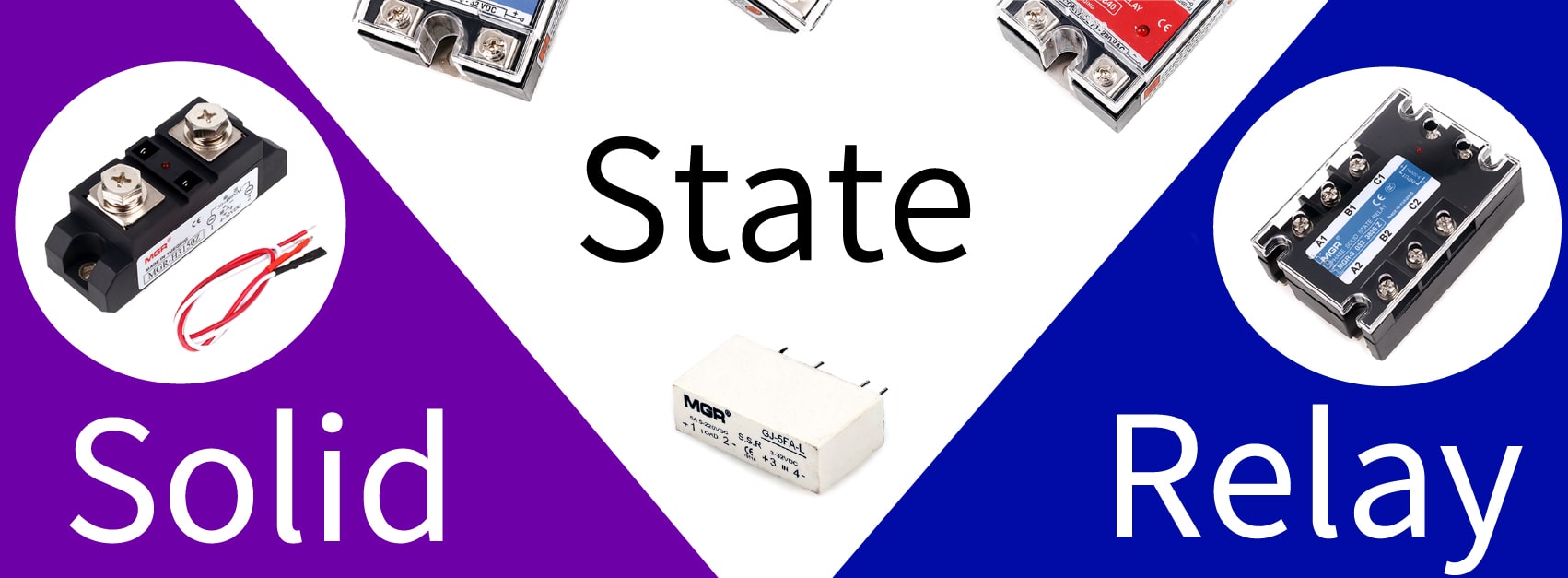
Solid State Relay (also known as SSR, SS Relay, SSR relay or SSR switch, solid-state contactor, power electronic switch, automotive relays, electronic power relays, and electrical signal contactors) is an integrated contactless electronic switch device that is compactly assembled from an integrated circuit (IC) and discrete components. Depending on the switching characteristics of the electronic components (such as switching transistors, bi-directional thyristors and other semiconductor components), the SSRs are able to switch the "ON" and "OFF" state of the load very quickly through the electronic circuit, just like the function of traditional mechanical relays. Compared with the previous "coil-reed contact" relay, namely Electromechanical Relay(EMR), there is no movable mechanical part inside the SSR, and there is also no mechanical action during the switching process of the SSR. Therefore, the Solid-State Relay is also called "non-contact switch".
The structural characteristics of the SSR switch make it superior to the EMR. The main advantages of solid state relays are as follows:
● The semiconductor component acts as a switch for the relay, which is small in size (compact size) and long in life (long lifetime).
● Better Electro-Magnetic Compatibility than EMR - immunity to Radio Frequency Interference (RFI) and Electro-Magnetic Interference (EMI), low electromagnetic interference, and low electromagnetic radiation.
● No moving parts, no mechanical wear, no action noise, no mechanical failure, and high reliability.
● No spark, no arc, no burning, no contact bounce, and no wear between contacts.
● With "zero voltage switching, zero current shutdown" function, easy to achieve "zero voltage" switching.
● Fast switching speed (SSR switching speed is 100 times higher than general EMR), high operating frequency.
● High sensitivity, low electrical level control signals (SSR can directly drive large current loads through the small current control signals), compatible with logic circuit (TTL, CMOS, DTL, HTL circuits), easy to implement multiple functions.
● Generally packaged by insulation material, with good moisture resistance, mildew resistance, corrosion resistance, vibration resistance, mechanical shock resistance and explosion-proof performance.
Furthermore, the amplification and drive function of the solid-state relay is very suitable for driving high-power actuator, which is more reliable than electromagnetic relays (EMR). The control switches of solid state relays require very low power, so the low control currents can be used to control high load currents. And, the solid-state relay uses mature and reliable optoelectronic isolation technology between the input and output terminals. This technology allows the output signal of the low power device to be directly connected to the input control terminals of the solid state relay, to control the high power device at the output terminal of the solid-state relay without the need for additional protection circuitry to protect the weak current device, because the "small control current device" (connected to the SSR input terminal) and the "large control power supplies" (connected to the SSR output terminal) have been electrically isolated. Besides, AC solid state relays use the "zero-crossing detector" technology to safely apply the AC-SSR to the computer's output interface without causing a series of interferences or even serious failures to the computer. And these features cannot be implemented by EMR.
Because of the inherent characteristics of solid state relays and the above advantages, SSR has been widely used in various fields since it came out in 1974, and has completely replaced electromagnetic relays in many fields where electromagnetic relays cannot apply. Especially in the computer automatic control system field, because the solid state relay requires very low drive power and are compatible with the logic circuit, and can also directly drive the output circuit without the need for an additional intermediate digital buffer.
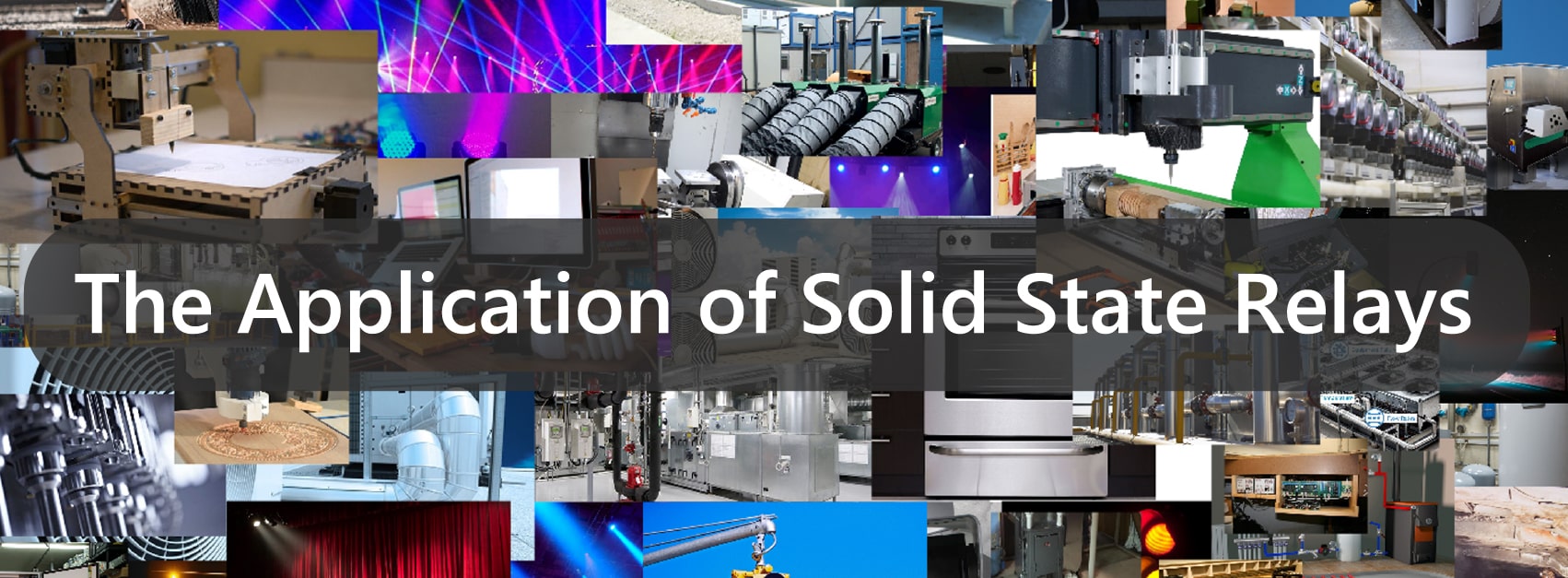
At present, solid state relays perform well in military, chemical, industrial automation control devices, electro mobile, telecommunication, civil electronic control equipment, as well as security and instrumentation applications, such as electric furnace heating system, computer numerical control machine (CNC machine), remote control machinery, solenoid valve, medical equipment, lighting control system (such as traffic light, scintillator, stage lighting control system), home appliances(such as washing machine, electric stove, oven, refrigerator, air conditioner), office equipment (such as photocopier,printers, fax machines and Multi-function printers), fire safety systems, electric vehicle charging system and so on. All in all, solid state relays can be used in any application requiring high stability (optical isolation, high immunity), high performance (high switching speed, high load current), and small package size.
Of course, solid state relays also have some disadvantages, including: exist on-state voltage drop and output leakage current, need heat dissipation measures, higher purchase cost than EMR, DC relays and AC relays are not universal, single control state, small number of contact groups, and poor overload capability. While some special customized solid state relays can solve some of the above problems, these disadvantages need to be considered and optimized when designing circuits and applying SSRs to maximize the benefits of solid state relays.
§2. What is the Structure of Solid State Relays
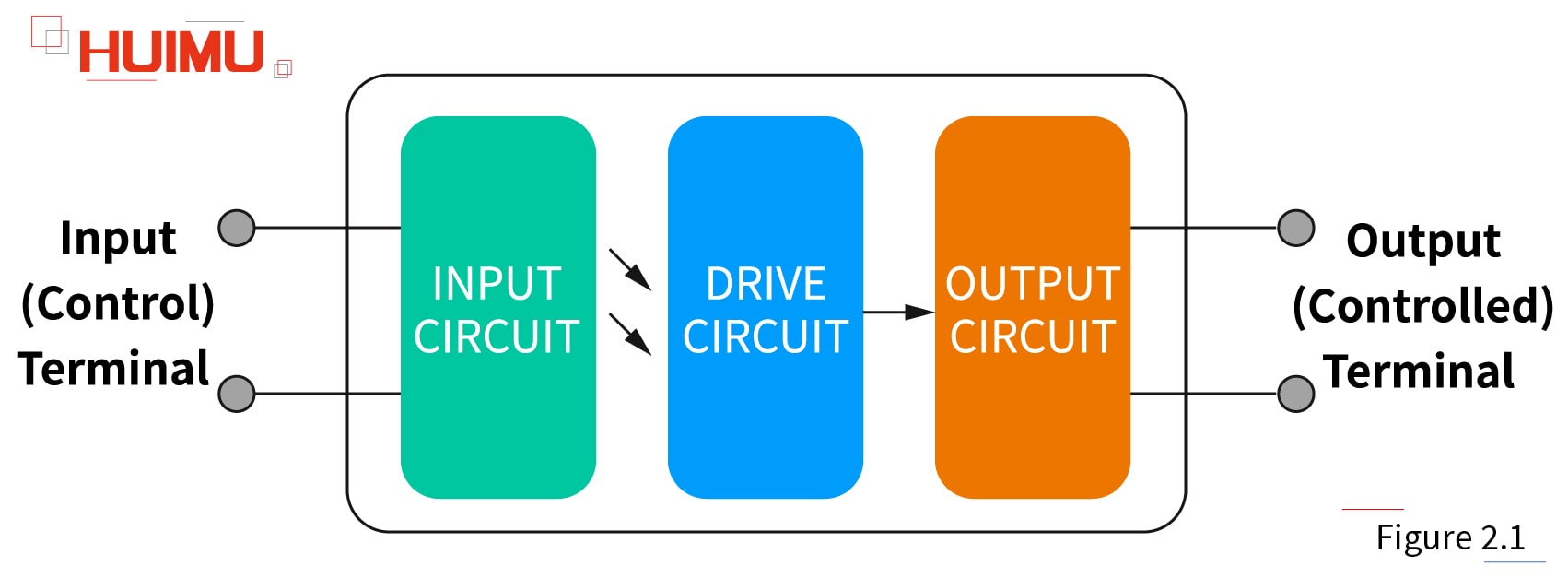
The solid-state relays are four-terminal active devices, two of the four terminals are input control terminals, and the other two terminals are output control terminals. Although the types and specifications of SSR switches are numerous, their structures are similar and consist mainly of three parts (as shown in Figure 2.1): Input Circuit (Control Circuit), Drive Circuit, and Output Circuit (Controlled Circuit).
Input Circuit:
The Input Circuit of the solid state relay, also called control circuit, provides a loop for the input control signal, making the control signal as a trigger source for the solid state relay. According to different input voltage types, the input circuit can be divided into three types, DC input circuit, AC input circuit and AC/DC input circuit.
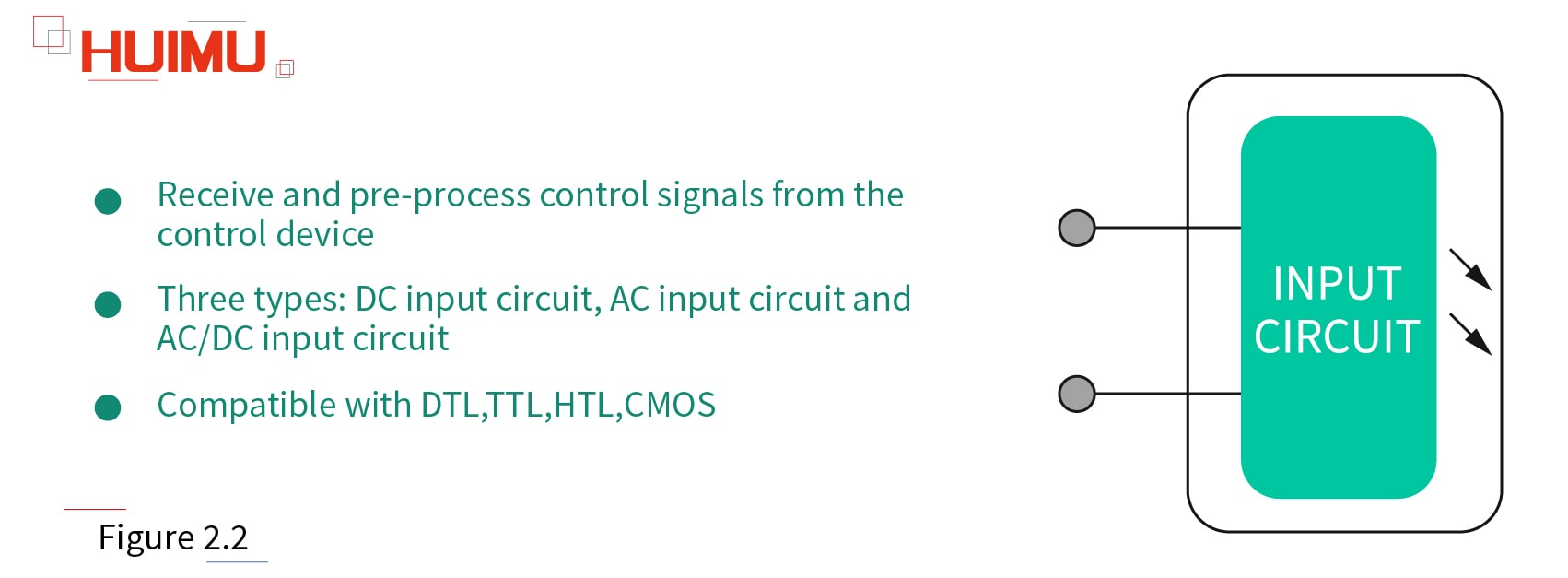
The DC input circuit can be further divided into Resistive Input Circuit and Constant Current Input Circuit.
1) The Resistive Input Circuit, whose input current increases linearly with increasing input voltage, and vice versa. If the control signal has a fixed control voltage, the resistor input circuit should be selected.
2) The Constant Current Input Circuit. When the input voltage of the constant current input circuit reaches a certain value, the current will no longer increase obviously as the voltage increases. This feature allows the use of a constant current input solid state relay over a fairly wide input voltage range. For example, when the voltage variation range of the control signal is kind of large (e.g., 3~32V), the DC solid state relay with constant current input circuit will be recommended to ensure that the DC solid-state relay can work reliably over the entire input voltage range.
Some of these input control circuits have positive and negative logic control, inverting and other functions, as well as the compatibility of logic circuits. Thus, solid state relays can be easily connected to TTL circuits (Transistor-Transistor Logic circuits), CMOS circuits (Complementary Metal Oxide Semiconductor circuits), DTL circuits (Diode-Transistor Logic circuits), and HTL circuits (High Threshold Logic circuits). At present, DTL has been gradually replaced by TTL, and HTL has been replaced by CMOS. And if the Pulse Width Modulated signal (PWM) is used as input signal, the ON/OFF switching frequency of the AC load supply should be set to less than 10Hz, or the output switching rate of the output circuit of the AC SSR cannot keep up with it.
Drive Circuit:
The driving circuit of solid state relay includes three parts: Isolation Coupling Circuit, Function Circuit and Trigger Circuit. However, according to the actual needs of solid-state relay, only one/two of these parts may be included.
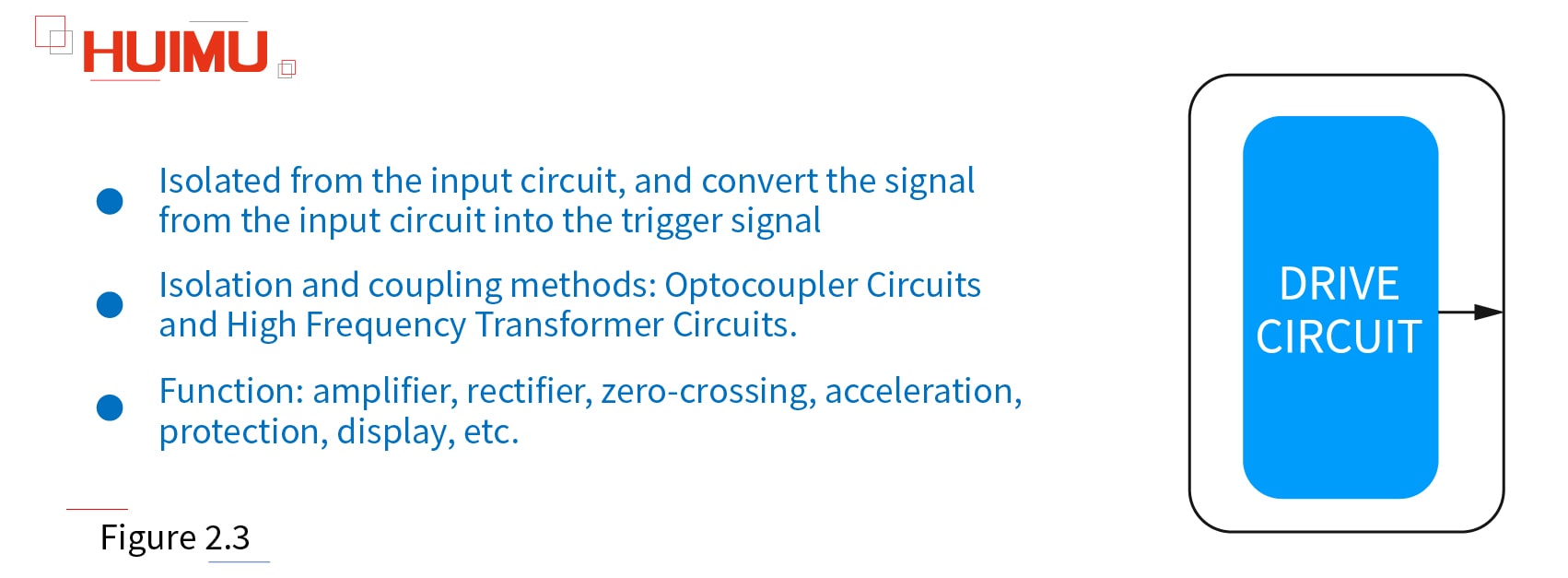
1. Isolated Coupling Circuit:
The isolation and coupling methods for I/O circuits (Input / Output circuit) of solid-state relays currently use two ways, Optocoupler Circuits and High Frequency Transformer Circuits.
1) Optocoupler (also called photocoupler, optical coupler, opto-isolator, or optical isolator) is opaquely packaged with an infrared LED (Light-Emitting Diode) and an optical sensor to achieve isolated control between "control side" and "load side", because there is no electrical connection or physical connection between the " Light emitter " and the " Light sensor" except the beam. The types of "source-sensor" combinations normally include: "LED-Phototransistor" (Phototransistor Coupler), "LED-Triac" (Phototriac Coupler), and "LED-Photodiode array" (the stack of photodiodes is used to drive a pair of MOSFETs or an IGBT).
2) The high frequency transformer coupling circuit uses a high frequency transformer to convert the control signal at the input to the drive signal at the output. The detail process is, the input control signal produces a self-oscillating high frequency signal that will be transmitted through the transformer core to the transformer secondary, and after processing by the detection/rectification circuit and the logic circuit, the signal will eventually become the drive signal to drive the trigger circuit.
2. Functional Circuit:
The functional circuit may include various functional circuits, such as detection circuit, rectifier circuit, zero-crossing circuit, acceleration circuit, protection circuit, display circuit, etc.
3. Trigger Circuit:
The trigger circuit is used to provide a trigger signal to the output circuit.
Output Circuit:
The output circuit of the solid-state relay is controlled by a trigger signal to enable on/off switching of the load power supplies.
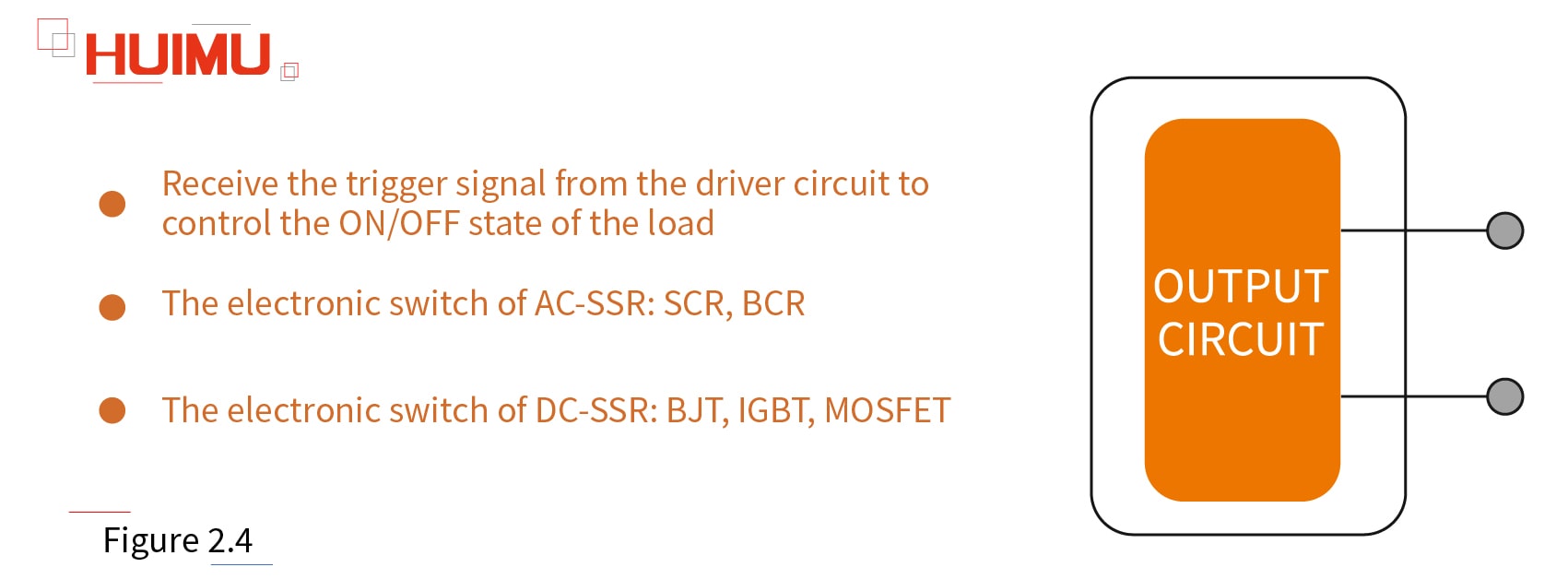
The output circuit is mainly composed of an output component (chip) and an absorption loop (which acts as a transient suppressor), and sometimes includes a feedback circuit. Up to now, the output component of solid state relays mainly include: Bipolar Junction Transistor (Bipolar Transistor or BJT, which divided of two types, PNP and NPN), Thyristor (Silicon Controlled Rectifier or SCR), Triac (Bi-directional Triode, Bi-directional thyristor, Bi-directional Controlled Rectifier or BCR), Metal-Oxide-Semiconductor Field-Effect Transistor (MOSFET), Insulated Gate Bipolar Transistor(IGBT), Silicon-Carbide MOSFET (SIC MOSFET, a kind of wide bandgap transistor with the industrial grade highest operating junction temperature of 200°C, low power consumption and compact size), and so on.
The output circuit of the solid state relay can be divided into three types: DC output circuit, AC output circuit and AC/DC output circuit. The DC output circuit typically uses bipolar component (such as IGBT or MOSFET) as the output component, and the AC output circuit usually uses two Thyristors or one Triac as the output component.
§3. What is the Symbol of Solid State Relays
The symbol of the solid-state relay in the circuit schematic is shown below (Figure 3.1).
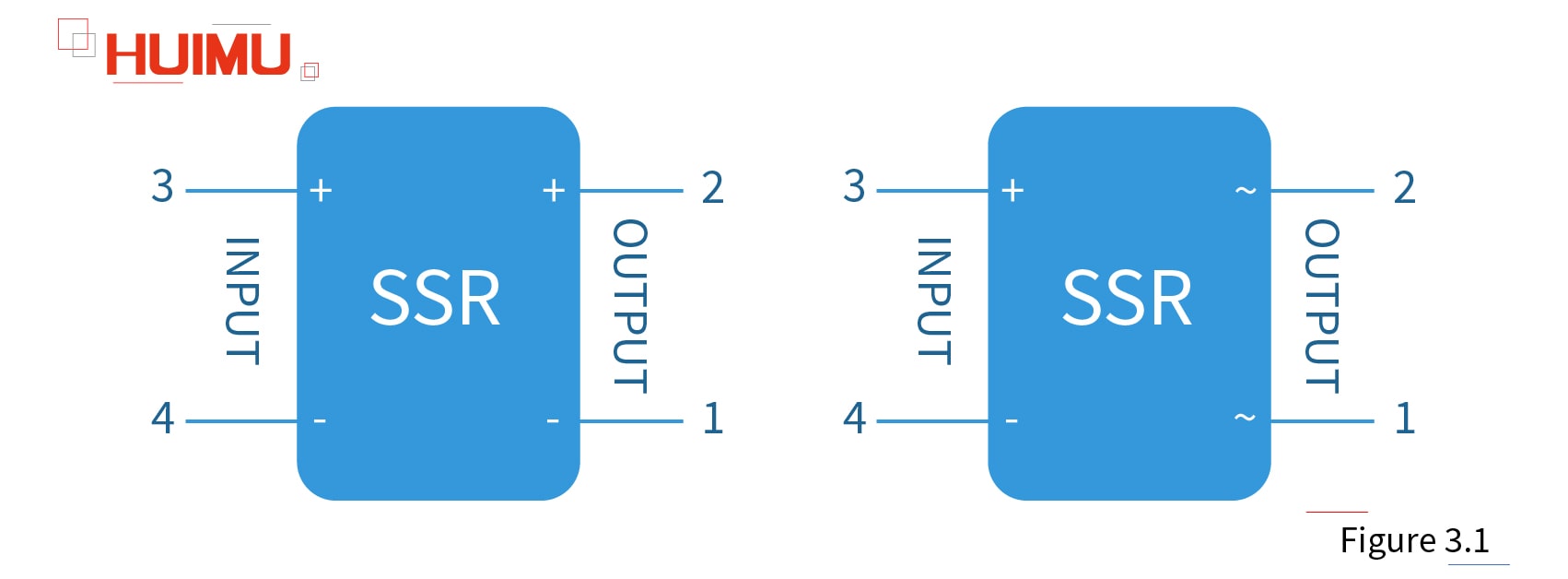
It should be noted that:
● The electrode symbol should be marked separately (inside or outside the frame) next to each pin of the graphic symbol.
● Input terminals and output terminals cannot usually be drawn on the same side or adjacent sides.
● When multiple solid state relays appear in the same circuit diagram, a numeric number can be added after the text symbol to distinguish the relays. (e.g. SSR1, SSR2).
§4. What are the Types of Solid State Relays
The types of solid state relays are various and the classification standards are multifarious. The solid state relays are usually classified according to the following criteria.
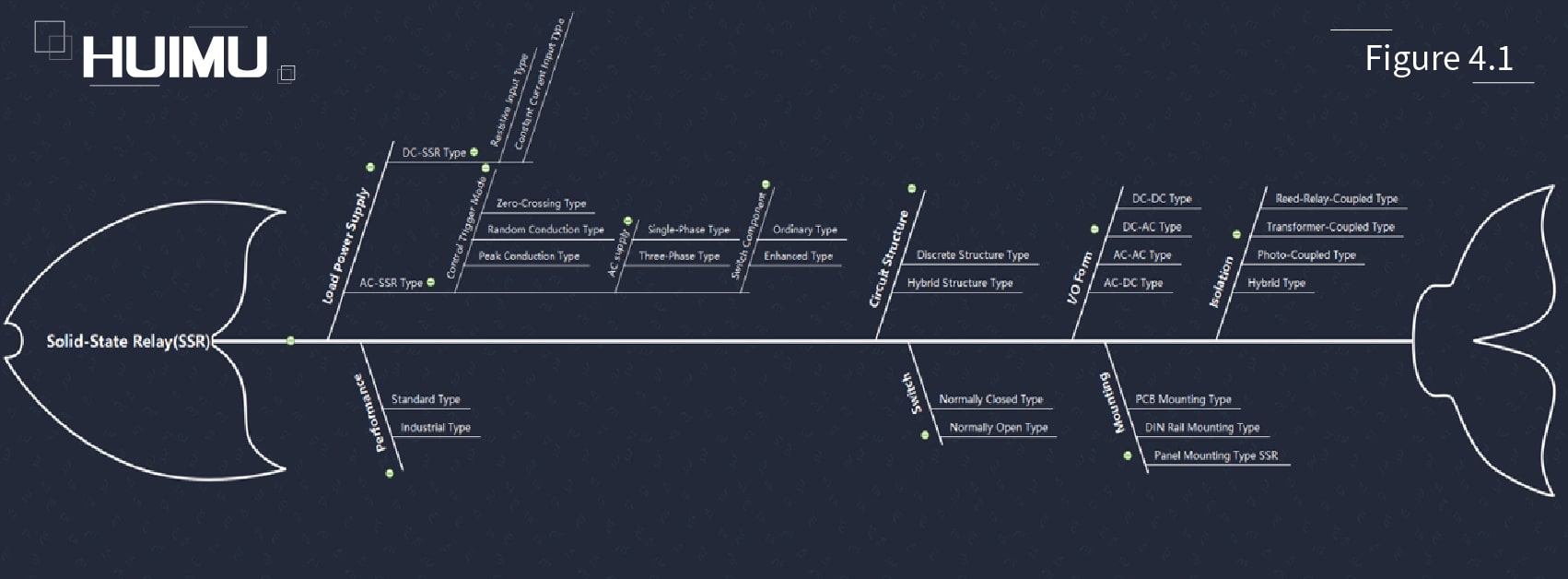
1. Load Power Supply Type:
The Solid-State Relay can be divided into DC solid state relays (DC-SSR) and AC solid-state relays (AC-SSR) according to the type of load power supply. The DC type solid state relays use the power semiconductor transistors as the switching element (such as BJT, MOSFET, IGBT) to control the ON/OFF state of the DC load power supply, and the AC type solid state relays use the thyristors (such as Triac, SCR) as the switching element to control the ON/OFF state of the AC load power supply.
1.1 DC-SSR:
Based on the input form, DC type SSR can be divided into the Resistive Input Type DC solid state relays and the Constant Current Input Type DC solid state relays.
1.2 AC-SSR:
The AC type SSR can be classified according to the following standards.
1.2.1 Control Trigger Mode:
According to the control trigger mode (the timing of turn-on and turn-off), the AC SSR can be divided into Zero-crossing Type AC solid state relays, Random Turn-on Type AC solid state relays, and Peak Turn-on Type AC solid state relays.
1) Zero-crossing AC solid state relays (Figure 4.2), are also known as Zero Crossing Trigger AC solid state relays, Zero cross turn-on solid state relay, Zero Switching AC solid state relays, Zero Voltage AC solid state relays, or Synchronous AC solid state relays. For the zero-crossing SSR relays, their switching state of the output circuit are synchronized with the output signal, that is, "synchronous" to the power supply. When the input signal turned on, if the load supply voltage is in the non-zero-crossing zone, the output terminal of the zero-crossing type solid state relays will not be switched on; but if the load supply voltage reaches zero zone, the output terminal of zero crossing SSR relay will be switched on, as well as, the load circuit will be turned on. This trigger mode can effectively reduce the inrush current generated during SSR turn-on, and also reduces the interference signal to the power grid and the input control circuit at the same time. In consequence, the zero-crossing solid state relays are the most common type in many fields.
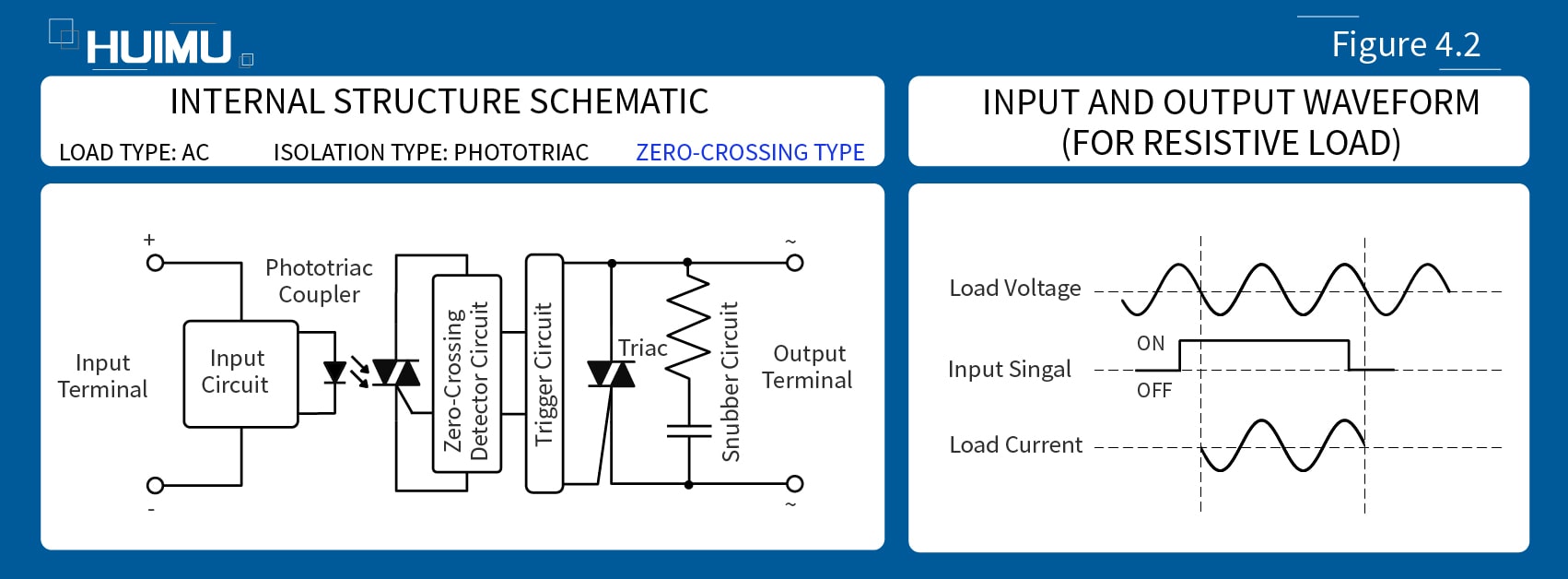
2) Random Turn-on Type AC solid state relays (Figure 4.3), are also known as Random Swtichng AC solid state relays, Random Switch On AC solid state relay, Random Conduction AC solid state relay, Random Fire AC solid state relay, Instantaneous Turn On solid state relay, Non-zero Switching AC solid state relays, Instant-on AC solid state relays, Instantaneous AC solid state relays, Asynchronous AC solid state relays or Phase Modulation AC solid state relays. The output circuit switching mode of the random type SSR relay is controlled only by the control signal and is independent of the power supply signal, i.e., "asynchronous" with the power supply. Random type solid state relays will be immediately turned on, as long as there are input signals in the input terminals, and regardless of the state of the load voltage. Since Random Solid-State Relay is turned on or off at any phase of the AC power source, a large interference signal may be generated at the turn-on instant.
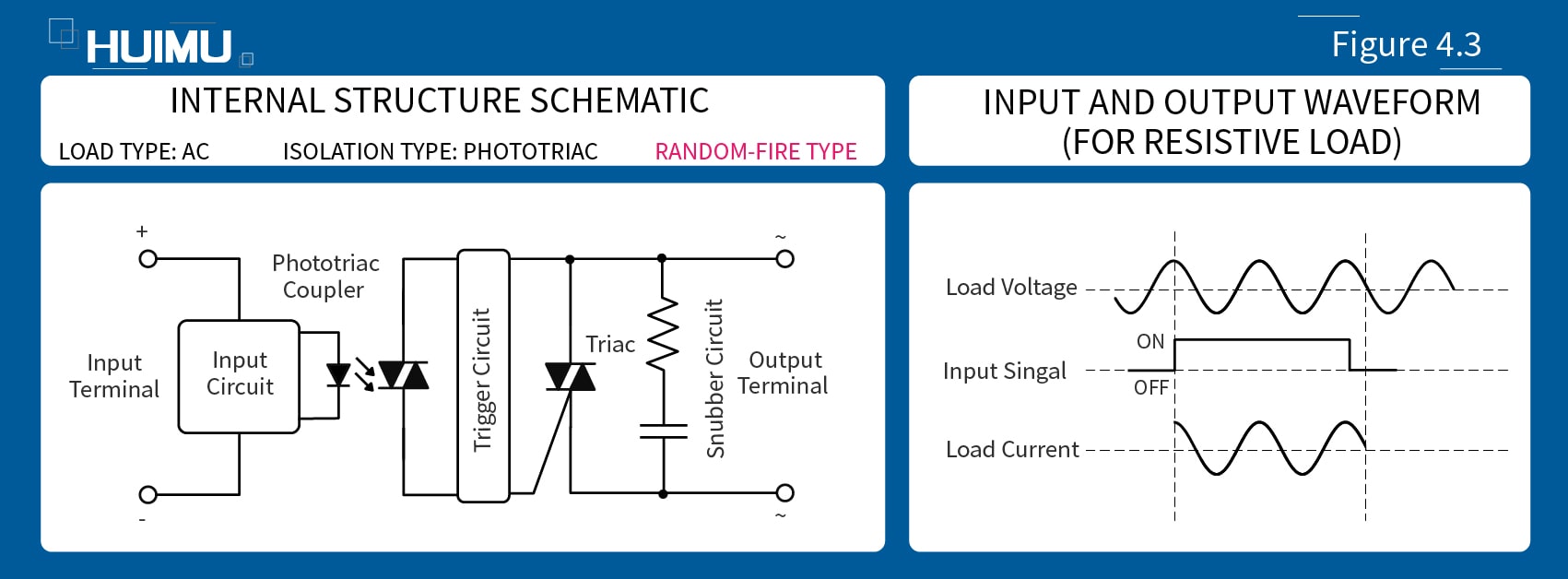
3) Peak Turn-on Type AC solid state relays are also known as Peak Switching AC solid state relays, or Peak Fire AC solid state relays. When the input control signal is applied, the peak type SSR relays are turned on at the first voltage peak point of the AC output voltage to reduce the inrush current; if the input control signal is removed, the Peak Solid State Relays will be turned off.
1.2.2 Phase:
According to the phase of the AC supply, the AC-SSR can be divided into the Single-Phase AC solid state relays and the Three-Phase AC solid state relays.
1) Based on the different function, single-phase AC solid state relays can be further divided into single-phase AC/DC solid-state relays,single-phase solid-state voltage regulators, single-phase solid-state governors,one open and one closed single-phase solid-state relays, single-phase forward and reverse solid state relays,single phase dual solid-state relays, and so on. It should be mentioned that the dual relay (Figure 4.4) which is a kind of single-phase solid-state relay that combines two single-phase industrial solid state relays into one standard industrial package with double input terminals and double output terminals, and each set of I/O terminals is independent of the other set, that is, the dual SSR relays have more contacts and can achieve more diverse control than the normal types.
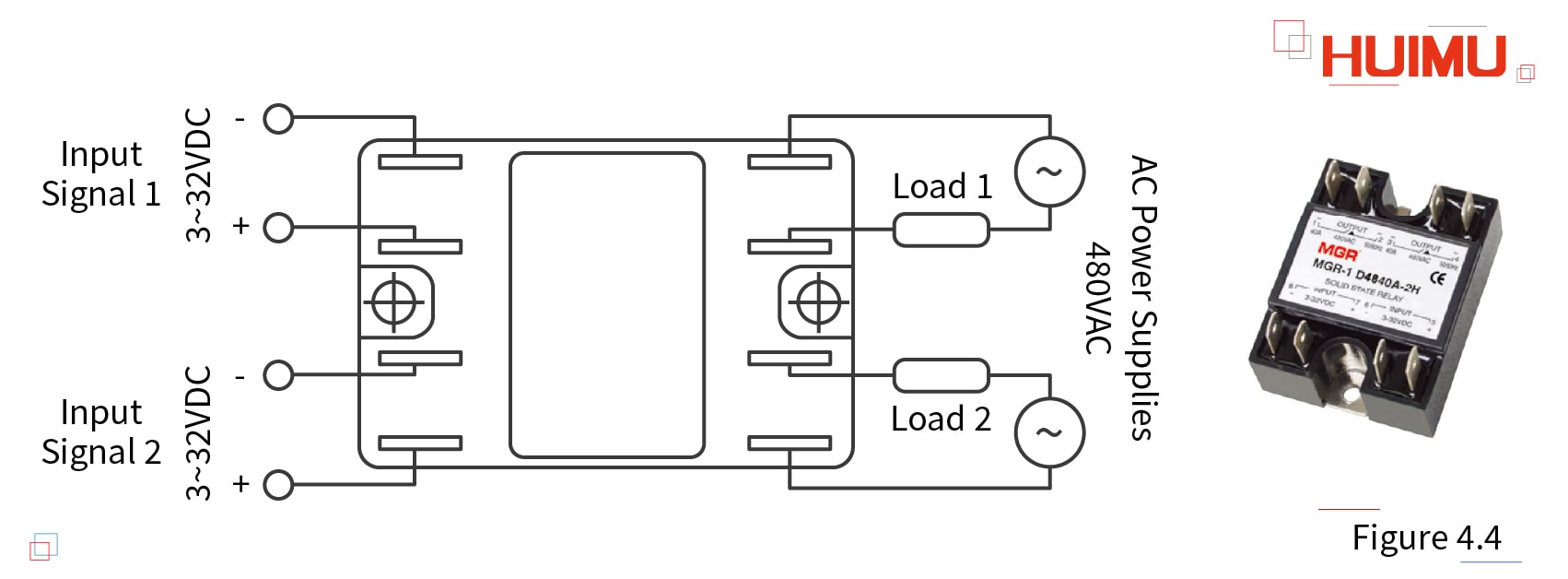
2) The three-phase AC solid state relays can be directly used for the control of three-phase AC motors, and the three-phase forward-reverse AC solid-state relay (or three-phase reversible AC solid-state relay) can be used to control the three-phase forward and reverse motors (three-phase bi-directional AC motors, or three-phase bi-rotational AC motors).
1.2.3 Switch Component:
According to switch components, the AC-SSR can be divided into the Ordinary Type AC solid-state relays and the Enhanced Type solid-state relays. The ordinary type SSR relays use the Triac as output switching component, and the enhanced type SSR relays used the SCR anti-parallel as the switching component.
2. I/O form:
According to the I/O form, the solid-state relays can be divided to four types: DC input-AC output type solid state relays (DC-AC SSR relays), DC input-DC output type solid state relays (DC-DC SSR relays), AC input-AC output type solid state relays (AC-AC SSR relays), AC input-DC output type solid state relays(AC-DC SSR relays).
3. Switch Type:
According to the switch type, the SSR switches can be divided into normally open type solid state relays (or NO-SSRs) and normally closed type solid state relays (or NC-SSRs). The normally open solid-state relays will be turned on, only when the input terminals are applied with the control signal. On the contrary, the normally closed solid state relays will be turned off, when the input signal is applied to the input terminal. (Unless otherwise specified, the solid state relays in this document refer to normally open solid state relays by default.)
4. Isolation/Coupling:
According to isolation/coupling methods, the SSR can be divided into Reed Relay Coupled type solid state relays, Transformer Coupled type solid state relays, Photo Coupled type solid state relays, and Hybrid type solid state relays.
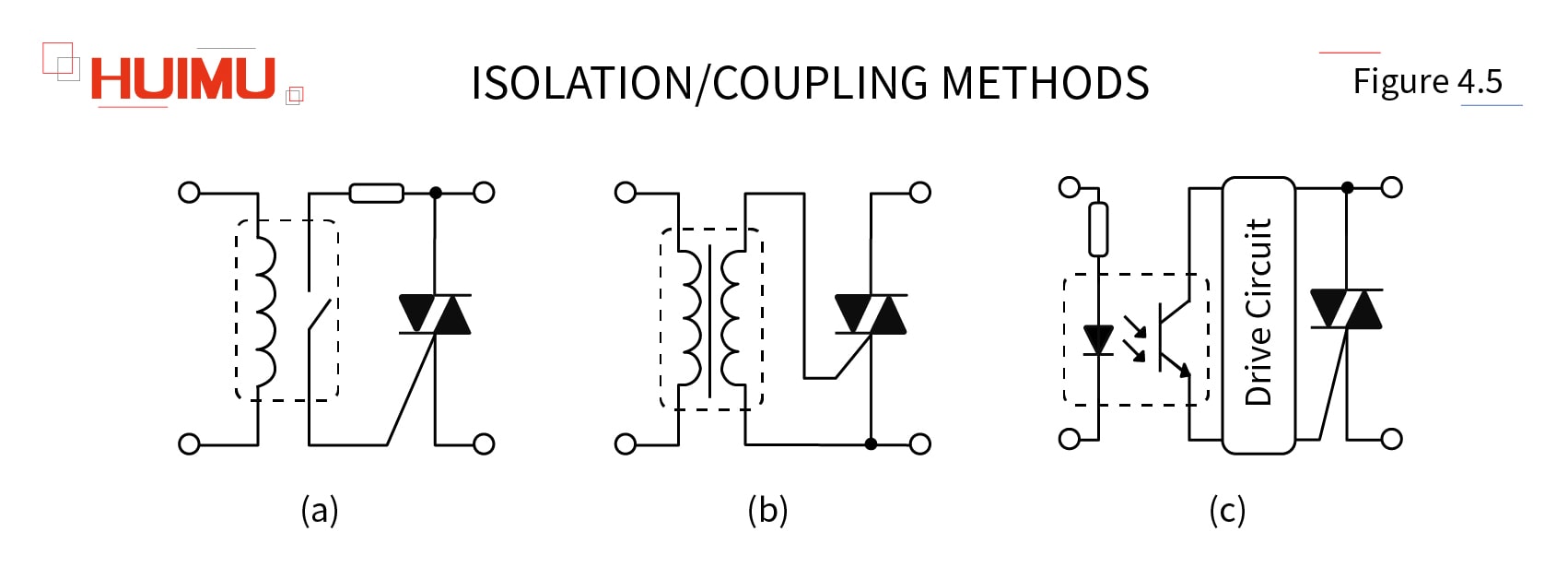
1) Reed Relay Coupling SSR (Figure 4.5, a) uses reed-switch as the isolation method. When the control signal is applied directly (or through the preamplifier) to the coil of the reed relay, the reed switch will close at once and the thyristor switch will be activated to make the load conduct.
2) Transformer Coupling SSR (Figure 4.5, b) uses a transformer as an isolation device. The transformer can convert the low power control signal from the primary coil to the secondary coil to generate a signal for driving the electronic switch. And if the input control signal is a DC voltage, a DC-AC converter is required in the input circuit. After processing by rectification, amplification or other modifications, the signal from the secondary coil can be used to drive the switching component.
3) Photo Coupling SSR (Figure 4.5, c), also known as photo-isolated SSR, or opto-coupled SSR, uses an optical coupler as an isolator. The optical coupler is an opto-isolator that consists of an infrared source (usually, a light-emitting diode, or LED) and a photo-sensitive semiconductor component (such as a photosensitive diode, a photo-sensitive transistor, and a photo-sensitive thyristor). According to the different components (Figure 4.6), the opto-coupler can be into Opto-Diode Coupler(Photo-Diode Coupler), Opto-Transistor Coupler (Photo-Transistor Coupler), Opto-SCR Coupler (Photo-SCR Coupler), and Opto-Triac Coupler (Photo-Triac Coupler).
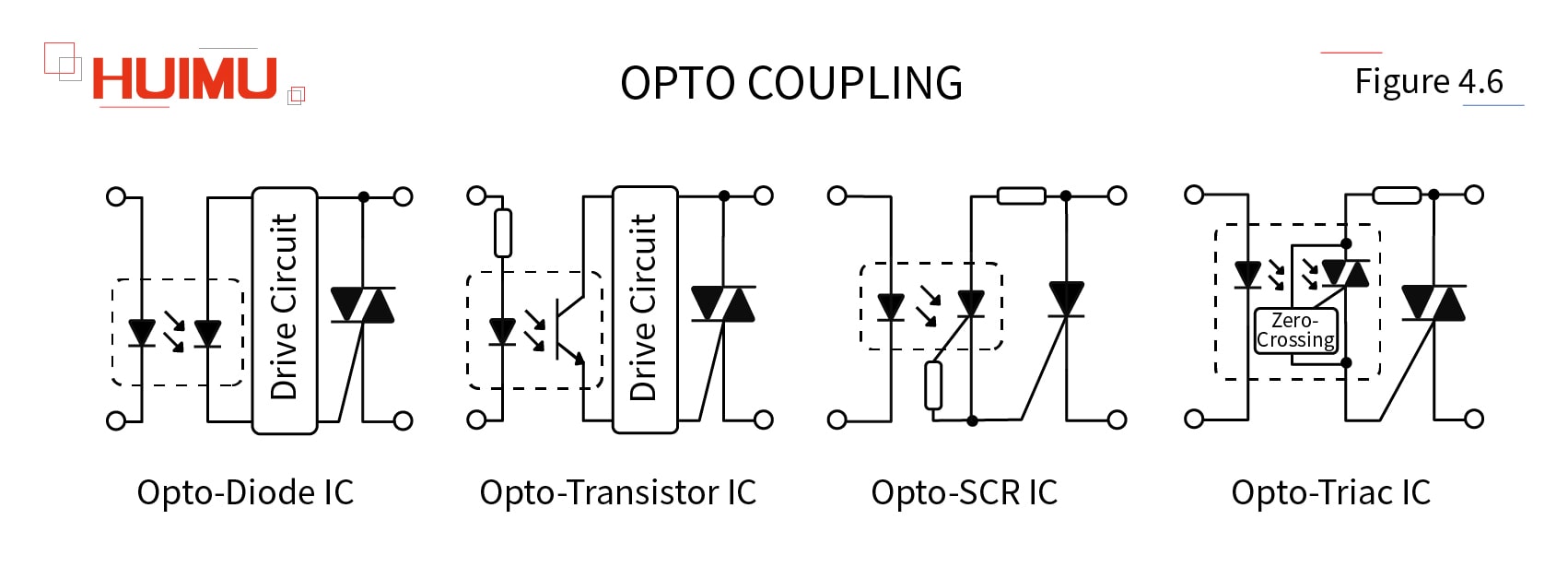
The photo-semiconductor device detects the infra-red radiation from the LED, and then produces a signal to drive the semiconductor switch. Compared with reed relay and transformer, the optical isolator has better physical isolation ability, to ensure the electrical insulation between high voltage output load circuit and low voltage input signal circuit. And on account of the excellent isolation performance and very compact size of the optocoupler, the optocoupler solid state relay is used in a very wide range of applications.
4) Hybrid solid state relay is a special solid state relay which combines the advantages of EMR and SSR, with high efficiency and low power consumption. The input and output circuits of the hybrid solid-state relays are composed of an SSR relay and a reed switcher (or a micro-electromagnetic relay) in parallel, controlled by different control signals (Figure 4.7).
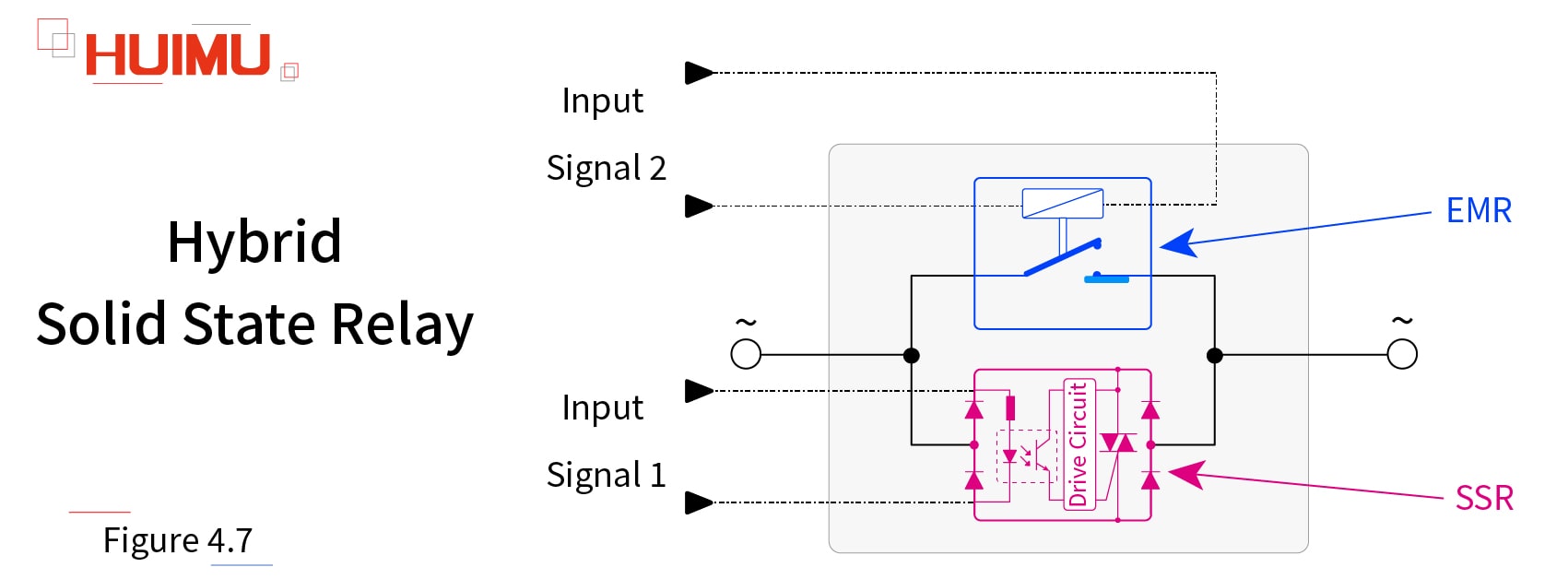
When Input Signal 1 is applied, the SSR immediately switches to the on state. Since the electronic switch has no moving parts, it can switch the load stably and quickly, and does not generate an arc due to high line voltage or heavy surge current during switching. After the load current is generated, the EMR will be controlled by the control signal 2 and switched on. Because the EMR is connected in parallel with the SSR, the output contact of the EMR is energized without voltage, and there is no arcing across the contacts. Then after a certain delay, the contact bouncing of the EMR settles down, and the SSR will be turned off. The EMR works almost with no heat, so the hybrid SSR relays can be run without a heat sink installed.
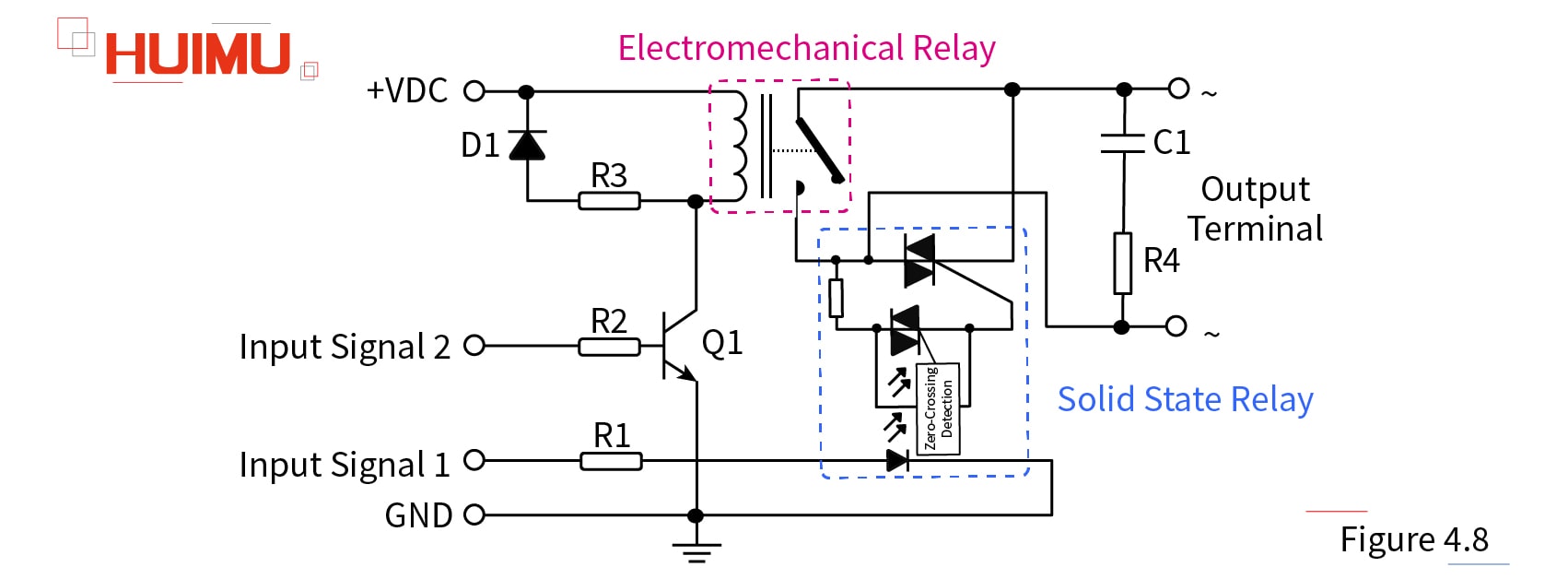
5. Circuit Structure:
According to different circuit structure, the solid-state relay can be divided into Discrete Structure Type solid state relays and Hybrid Structure Type solid state relays. The discrete structure solid state relays are mostly assembled by discrete components and printed-circuit board, and then packaged by epoxy resin potting, plastic sealing or resin wrapping. The hybrid structure solid state relays use thick-film combine technology to assemble discrete components and semiconductor integrated circuits (IC), and then encapsulate them in a metal or a ceramic housing.
6. Performance:
According to the performance, the solid-state relay can be divided into the Standard Type solid state relays, and the Industrial Type solid state relays. The rated current of the standard solid-state relay is generally 10A to 120A, and the rated current of the industrial solid-state relay is relatively large, can be 60A to 2000A or larger. Therefore, the industrial SSR relay can meet the strict requirements of the industrial environment and industrial machinery.
7. Mounting:
According to the mounting methods, the solid-state relays can be divided into Panel Mounting Type solid state relays (or Surface Mounting Type), DIN Rail Mounting Type solid state relays, and Printed Circuit Board Mounting Type solid state relays (or PCB Mounting Type). And the PCB mounting SSR can be further divided into Socket Mounting Type SSR (or Plug-in Mounting Type) and Bracket Mounting Type SSR (or Flange Mounting Type). The plug-in solid-state relays with many package standard (like SIP, Mini-SIP, and DIP), can be directly soldered on the printed circuit board, relying on natural cooling, without the need for a heat sink; the flange mounting solid state relays require the additional metal plate or heat sink to dissipate heat.
8. Application:
According to the application, the solid state relays can be divided into General Application Solid State Relays, Two-way Transmission Solid State Relays, Automotive Solid-State Relays, Latching Solid State Relays (the input signal runs as a logical
Exclusive OR, or XOR, so any input can latch/unlatch the output), and so on.
The latching relay can keep conducting and continuously output the control signal even if cutting off the control current, and it can only be turned off by inputting the reverse current or the off button. The latching is usually used in high-voltage circuits to avoid the expansion of accidents.
§5. What are the Basic Parameters of Solid State Relays
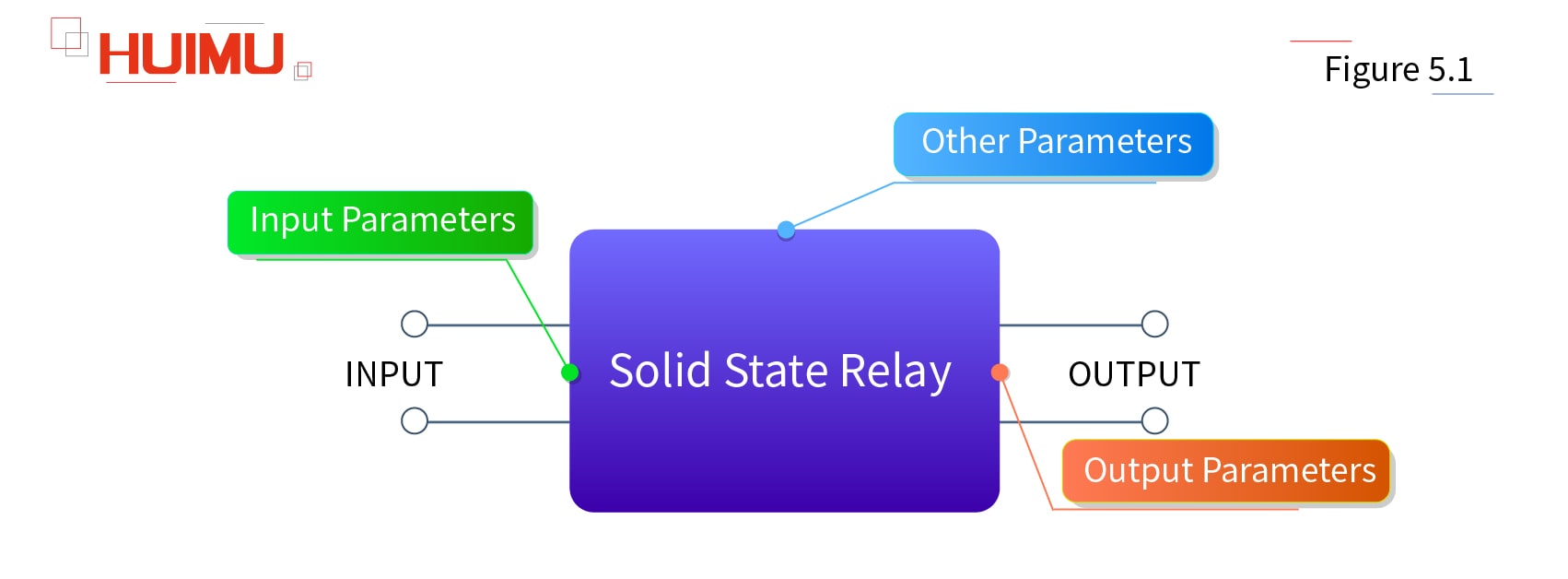
The basic parameters of solid-state relays fall into three categories: Input Parameters, Output Parameters and Other Parameters.
Input Parameters:
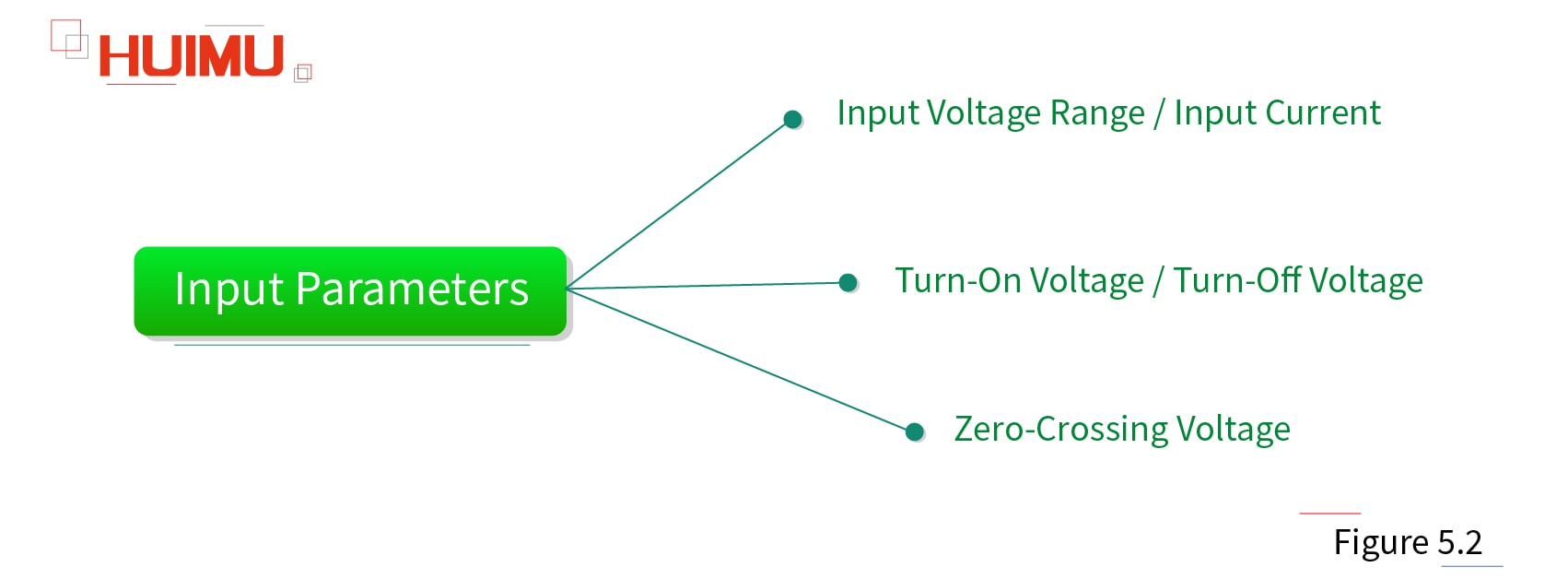
Input Voltage Range / Input Current:
1) The input voltage range refers to the voltage range value that must be input (i.e. minimum) or allowable input (i.e. maximum) for the solid-state relay to operate normally when ambient temperature is at 25 °C.
2) Input current refers to the corresponding input current value at a specific input voltage.
Turn-On Voltage / Turn-Off Voltage:
1) The turn-on voltage (switch-on voltage). When the input voltage (the voltage applied to the input terminal) is greater than or equal to the turn-on voltage, the output terminal will be turned on.
2) Turn-Off Voltage (switch-off voltage). When the input voltage (the voltage applied to the input terminal) is less than or equal to the shutdown voltage, the output terminal will be turned off.
Zero-Crossing Voltage:
Strictly speaking, the zero-crossing voltage is not a voltage point but a voltage range that determined by the internal components of the zero-crossing relay, which is typically very low and almost negligible. If the power supply voltage is below the zero-crossing voltage, the zero crossing relay will not be turned on; and if the voltage is beyond the zero-crossing voltage, the zero crossing relay will be in the on-state.
Output Parameters:
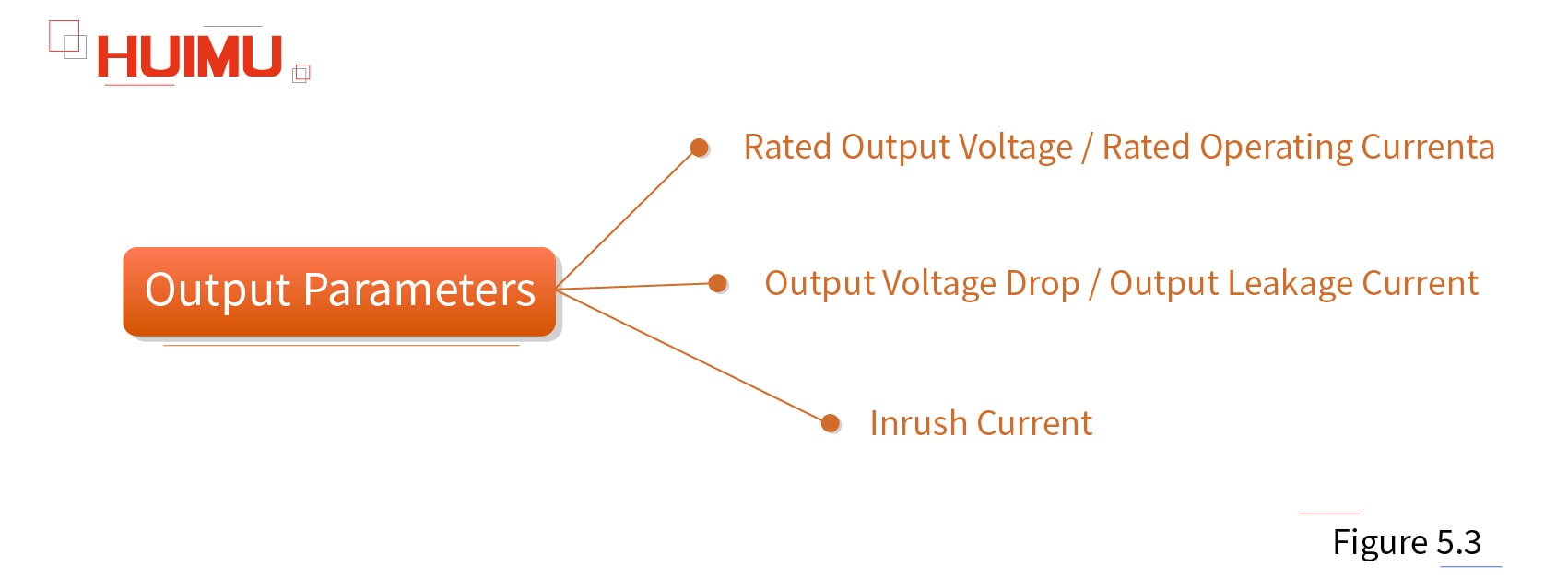
Rated Output Voltage / Rated Operating Current:
1) The rated output voltage is the highest load operating voltage that the output terminals can withstand.
2) The rated operating current is the maximum steady-state operating current that can pass through the output terminals at an ambient temperature of 25 °C.
Output Voltage Drop / Output Leakage Current:
1) The output voltage drop is the measured output voltage at the rated operating current when the solid-state relay is in the on state.
2)
The output leakage current refers to the measured current value that flowing through the load, under the condition that the solid-state relay is in the
off state and the rated output voltage is applied to the output terminal.
This parameter is an indicator of the quality and performance of solid-state relays. The smaller the output voltage drop and the output leakage current, the better the solid-state relay.
Inrush Current:
Inrush current, also known as overload current, input surge current, or switch-on surge current, refers to the non-repetitive maximum (or overload) current value that the device will not be permanent damage and the output terminals can withstand, when the solid-state relay is in the on-state. The inrush current of the AC SSR is 5~10 times (in one cycle) of the rated operating current, and the DC SSR is 1.5~5 times (in one second) of the rated operating current.
Other Parameters:
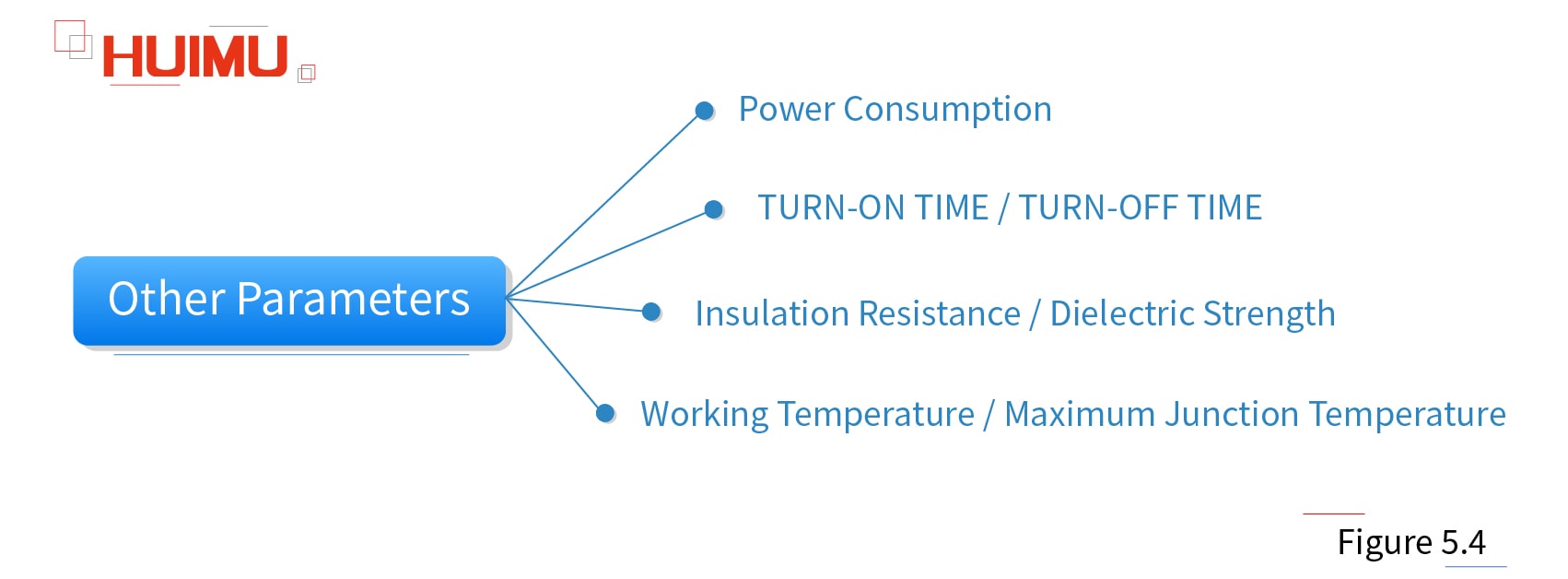
Power Consumption:
Power Consumption, refers to the maximum power value consumed by the solid-state relay itself in the power-on state and the power-off state.
Switching-on Time / Switching-off Time:
1) The switching-on time (or turning-on time) is the time it takes for a normally open solid state relay to start from being applied the input control voltage until the output terminal begins to switch on and the output voltage reaches 90% of the final variation.
2) The switching-off time (or turning-off time) is the time it takes for a normally open solid state relay to start from being cut off the input control voltage until the output terminal begins to switch off and the output voltage reaches 90% of the final variation.
This is also an important parameter to judge the performance of solid-state relays. The shorter the turn-on time and the turn-off time, the better the switching performance of the solid-state relay.
Insulation Resistance / Dielectric Strength:
1) Insulation resistance refers to the measured resistance value between the input terminal and the output terminal of the solid-state relay when a certain DC voltage (for example, 550V) is applied. It can also include the measured resistance value between the input terminal and the outer casing (including the heat sink), and the measured resistance value between the output terminal and the housing.
2) Dielectric Strength, or dielectric withstand voltage, refers to the maximum voltage value that can be tolerated between the input terminal and the output terminal of the solid-state relay. It can also include the maximum voltage that can be tolerated between the output terminal and the housing, and the maximum voltage that can be tolerated between the input terminal and the outer casing.
Operating temperature / Maximum Junction Temperature:
1) Operating temperature refers to the normal working environment temperature range allowed when the solid-state relay installs the heat sink according to the specification, or when the heat sink is not installed.
2) Junction temperature, short for transistor junction temperature, is the actual operating temperature of a semiconductor in an electronic device. In operation, it is usually higher than the case temperature and the external temperature of the component. The maximum junction temperature is the highest junction temperature allowed by the output switching component.
§6. What is the Working Principle of Solid-State Relays
Through this chapter you will learn how do solid state relays work. Because of the different application environments, solid-state relays have slightly different internal components, but the working principle is similar. The internal equivalent circuit diagram of ordinary solid-state relays is shown in the figure below (Figure 6.1). The principle of solid-state relays can be simply described as: for the NO-SSR, when the appropriate control signal is applied to the Input Terminal (IN) of the solid-state relay, the Output Terminal (OUT) will be switched from the off state to the on state; if the control signal is cancelled, the Output Terminal (OUT) will be restored to the off-state. In this process, the solid state relays realize non-contact control of switch states of the load power supply which is connected to output terminals. It should be noted that the input terminal can only be connected to the control signal, and the load should only be connected to the output circuit.
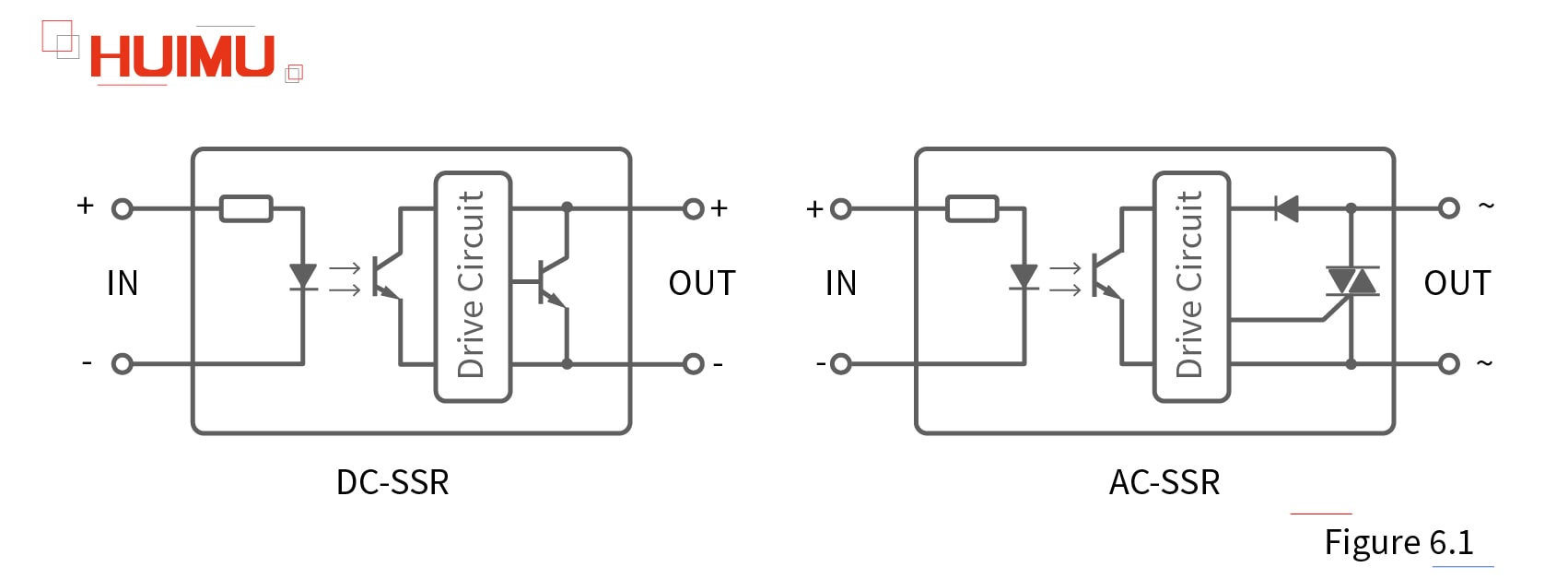
According to the type of load, SSR can be divided into two types: DC Solid State Relay (DC-SSR) and AC Solid State Relay (AC-SSR). The DC-SSRs act as a load switch on the DC power supplies, and the AC-SSRs act as a load switch on the AC power supplies. They are not compatible with each other and cannot be mixed.
1) DC solid state relay (Figure 6.1, Left), whose control signal voltage is inputted from the Input Terminal (IN), and then the control signal is coupled to the receiving circuit through the photocoupler, and eventually the signal is amplified by the amplifier to drive the switching state of the Transistor. Obviously, the Output Terminal (OUT) of the DC solid state relay is divided into Positive Terminal (+ pole) and Negative Terminal (- pole), be careful not to make mistakes when connecting the output terminal of DC SSR relay to the controlled circuit.
2) AC solid state relay (Figure 6.1, Right), is used to control the ON/OFF state of the AC load circuit. Unlike DC solid-state relays, the AC SSR relays use the bidirectional thyristor (Triac) or other AC electronic switching components. Therefore, there is no Positive/Negative Terminal in the Output Terminal (OUT) of the AC solid state relay.
The working principle of Zero-Crossing AC Solid-State Relays
Since zero-crossing AC solid state relays are completer and more typical than other types of solid state relays, the operation details of AC zero-crossing SSR relays can help illustrate the complete working principle of SSR relays:
1. The Function of Each Parts:
Following is the representation of the AC zero-crossing SSR (Figure 6.2). And the A~E circuit in the block diagram forms the body of the Zero-Crossing AC SSR. On the whole, the SSR relay is a four-terminal load switch, with only two input terminals (③ and ④) and two output terminals (①and ②). When the AC Zero-Crossing SSR relay is working, as long as a certain control signal is added to ③ and ④ terminals, the ON/OFF state of the loop that between the ① and ② terminals can be controlled.
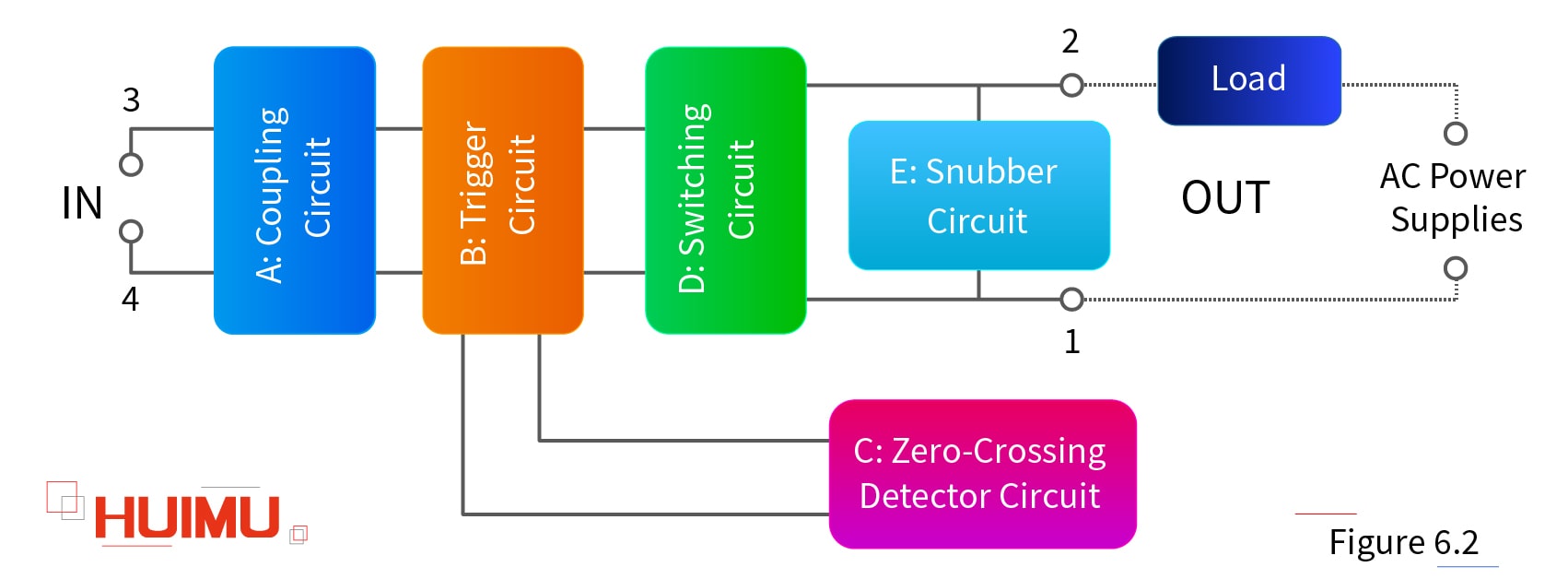
The Coupling Circuit A is used to provide an I/O channel for the control device that connected to the ③ and ④ terminals, and electrically cut off the connection between the input terminals and output terminals of the SSR to prevent the
output circuit from interfering with the input circuit. The most commonly used component in the coupling circuit is the optocoupler with high action sensitivity, high response speed, and high dielectric strength (withstand voltage) between the
input and output terminals. Since the input load of the photo-coupler is a light emitting diode (LED), this makes the input value of the solid-state relay easy to match the input signal level of the control device, and make it possible to connect
the input terminals of the SSR relays directly to the computer output interface, that is, the solid state relay can be controlled by the logic level of "1" and "0".
The function of the Trigger Circuit B is to generate a suitable trigger
signal to drive the Switching Circuit D to operate. However, if no special control circuit is added, the switching circuit will generate Radio Frequency Interference (RFI), which will pollute the grid by the higher harmonics and the spikes,
so the Zero-Crossing Detector Circuit C is specifically designed to solve this problem.
The Snubber Circuit E is designed to prevent spikes and surges from the power supply from causing impacts and disturbances (even malfunctions)
to the switching transistors. Generally, an RC circuit (resistor–capacitor circuit, or RC filter or RC network) or a non-linear resistor (such as varistor) is used as the snubber circuit. The varistor,
also called voltage-dependent resistor (VDR), is an electronic component whose resistance value varies nonlinearly with the applied voltage, and the most common type of varistor is the metal-oxide varistor (MOV), such zinc oxide nonlinear resistor (ZNR).
2. The Function of Each Components:
The figure below is the internal schematic diagrams of the zero-crossing trigger type AC-SSR (Figure 6.3)
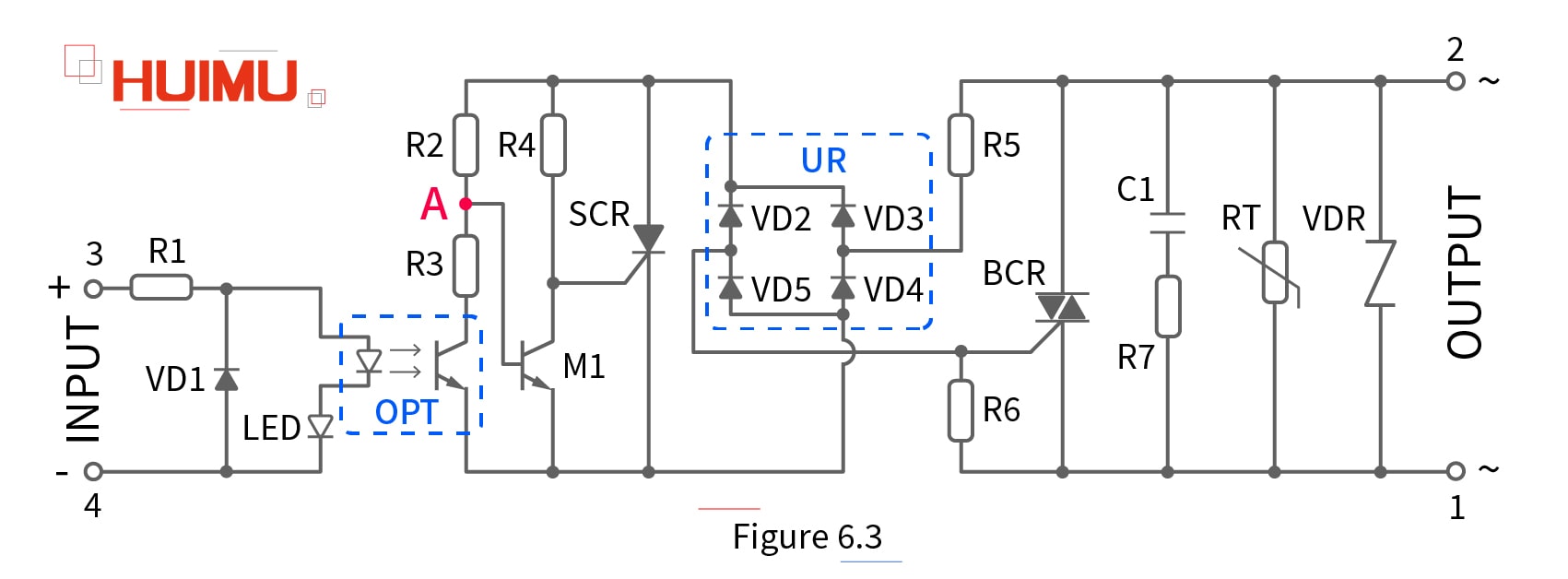
R1 is a current limiting resistor that limits the input signal current and ensures that the optocoupler is not damaged. LED is used to display the input state of the input control signal. The diode VD1 is used to prevent the optocoupler from being damaged when the positive and negative poles of the input signal are inverted. The optocoupler OPT electrically isolates the input and output circuits. The triode M1 acts as an inverter, and constitute the zero-crossing detection circuit with the thyristor SCR at the same time, and the operating state of the SCR thyristor is determined by the alternating-voltage zero-detection transistor M1. VD2~VD4 form the full-wave rectifier bridge (or full-wave diode bridge) UR. A bidirectional trigger pulse for turning on the triac BCR can be obtained from SCR and UR. R6 is a shunt resistor used to protect the BCR. R7 and C1 make up a surge absorbing network to absorb spike voltage or surge current in the power mains to prevent shock or interference to the switching circuit. RT is a thermistor that acts as an overheating protector to prevent solid state relays from being damaged due to excessive temperatures. VDR is a varistor that acts as a voltage-limiting device that clamp the voltage and absorbs excess current to protect the solid-state relay when the output circuit is overvoltage.
3. The Process of Working:
The AC zero-crossing solid state relay has the characteristics of being turned on when the voltage crosses zero and being turned off when the load current crosses zero.
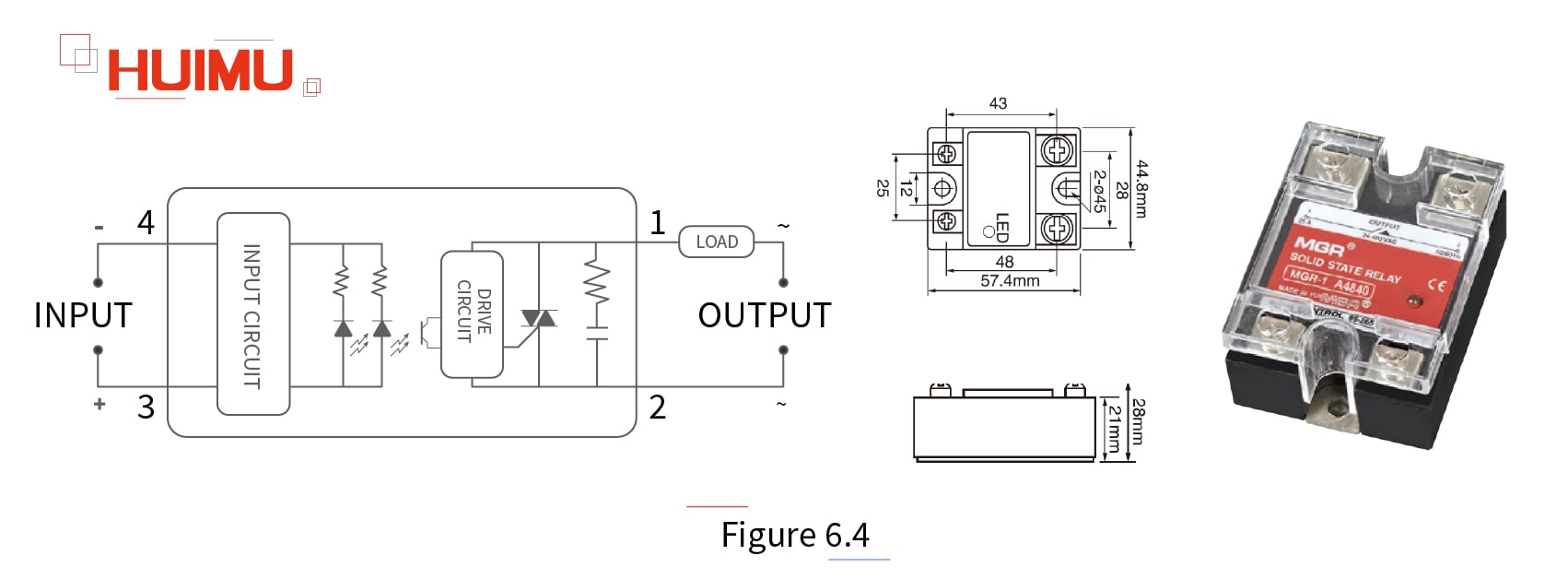
When the opto-coupler OPT is turned off (i.e. the control terminal of OPT has no input signal), M1 is saturated and turned on by obtaining the base current from R2, and as a result, the gate trigger voltage (UGT) of the thyristor SCR is clamped
to a low potential and turned off. Consequently, the triac BCR is in the off state because there is no trigger pulse on the gate control terminal R6.
When an input control signal applied on the input terminal of the solid-state relay, the
phototransistor OPT is turned on (i.e. the control terminal of the OPT has an input signal). After the power mains’ voltage is voltage-divided by R2 and R3, if the voltage at point A is larger than the zero-crossing voltage of M1 (i.e. VA>VBE1),
M1 will be in the saturated conduction state, and both SCR and BCR thyristors will be in the off state. If the voltage at point A is less than the zero-crossing
voltage of M1 (i.e. VA<VBE1), M1 will be in the cut-off state, and the SCR will be triggered to conduct, and then the trigger pulse from "R5→UR→SCR→UR→R6" direction (or the opposite direction) is obtained on the control pole of the BCR to
activate the BCR, and finally the load will be connected to AC mains.
Through the above process, it can be understood that M1 is used as an AC voltage detector for turning on the solid-state relay when the load voltage crosses zero and turning
off the solid state relay when the load current crosses zero. And on account of the function of the zero-crossing detector, the impact of the load circuit on the load is correspondingly reduced, and the radio frequency interference generated
in the control loop is also greatly reduced.
4. The Definition of Zero-Crossing:
Here it need be explained what is the zero crossing. In the alternating current, the zero-crossing is the instantaneous point at which there is no voltage present, that is, the junction between the positive half cycle and the negative half cycle
of the AC waveform. In each cycle of alternating current, there will usually be two zero crossings. And if the power mains switches at the instant point of zero crossing, no electrical interference will be generated. The AC solid-state relay
(equipped with a zero-crossing control circuit) will be in the ON state when the input terminal is connected to the control signal and the output AC voltage crosses zero; conversely, when the control signal is turned off, the SSR be in the OFF
state until the next zero crossing.
In addition, it should be pointed out that the zero crossing of solid state relay does not actually mean zero volts of the power supply voltage waveform. Figure 6.5 is a section of the AC voltage sine
wave. According to the characteristics of the AC switching component, the AC voltage in the figure is divided into three regions that correspond to three states of the SSR’s output circuit. And U1 and U2 respectively represents the threshold voltage and the saturation voltage of the switching component.
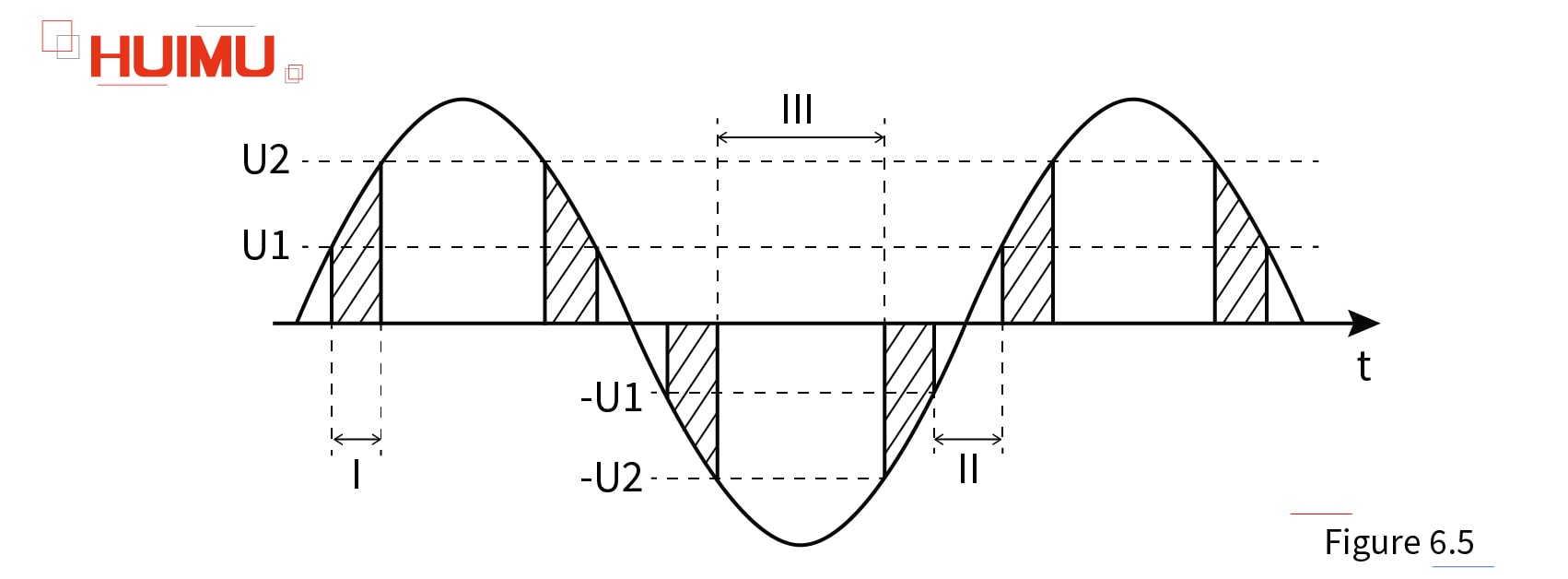
1) Region Ⅰ is the Dead Region (Cut-Off Region, Cut Out Region, or Turn Off Region), with an absolute value of voltage range of 0~U1. And in this zone, the SSR switch cannot be turned on, even if an input signal is added.
2) Region Ⅱ is the Response Region (Active Region, Cut-On Region, Cut In Region, or Turn On Region) with an absolute value of voltage range of U1~U2. In this zone, the SSR is immediately turned on, as soon as the input signal is added, and the output voltage increases as the supply voltage increases.
3) Region Ⅲ is the Suppression Region (Saturation Region) with an absolute value of voltage range greater than U2. In this region, the switching element (thyristor) is in the saturated state. And the output voltage of the solid-state relay will no longer increases with the increase of the power supply voltage, but the current increases with increasing voltage, which can be regarded as an internal short circuit state of the output circuit of the solid-state relay, that is, the solid-state relay is in the Switch-On state as an electronic switch.
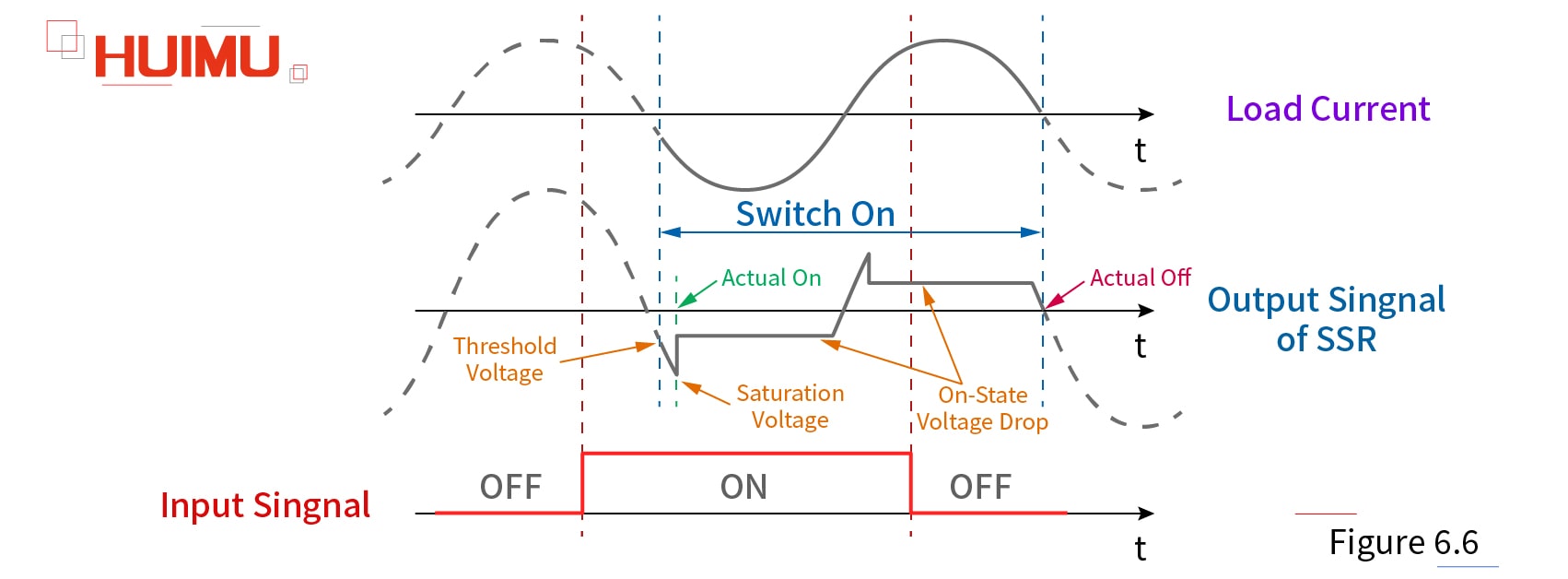
Figure 6.6 shows the I/O waveform of the zero-crossing solid-state relay. And because of the nature of the thyristor, the solid-state relay will be in the on state after the voltage of the output terminals reaching the threshold voltage (or the trigger voltage of the trigger circuit). Then the solid-state relay will be in the actual on state after reaching the saturation voltage, and at the same time, generate a very low on-state voltage drop. If the input signal is turned off, the solid-state relay will be switched off when the load current drops below the thyristor’s holding current or the next AC commutation point (i.e. the first time the load current passes through zero after the SSR relay turned off).
§7. What is the Application of the Solid State Relays
Through this chapter you will learn where to use solid state relays and what is solid state relay used for.
Lighting Control System:
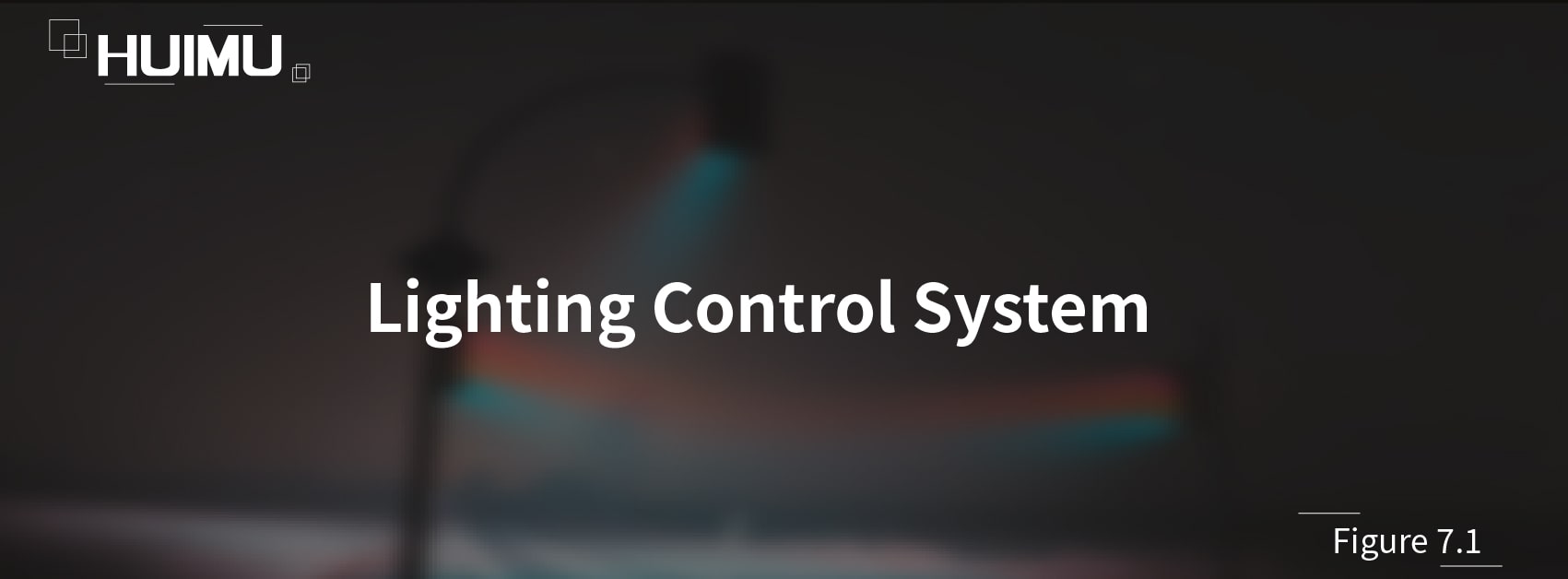
The fast switching, long life and high reliability of solid-state relays make themselves excellent in the light control system. In the field of traffic lights, the working environment of traffic lights is complicated, but solid-state relays with excellent characteristics (moisture proof, explosion-proof, anti-corrosion) can face it. And the solid-state relays can meet the requirements for sign/signal flashing traffic lights which are frequently closed and open, because they can maintain switching intervals of 10 milliseconds or longer. And in stage lighting control systems (usually applied to the production of theatre, dance, opera and other performance arts), solid state relays can work with the computer system to control multiple lights, and implement complex lighting effects to increase the atmosphere of the stage.
Remote Control System:
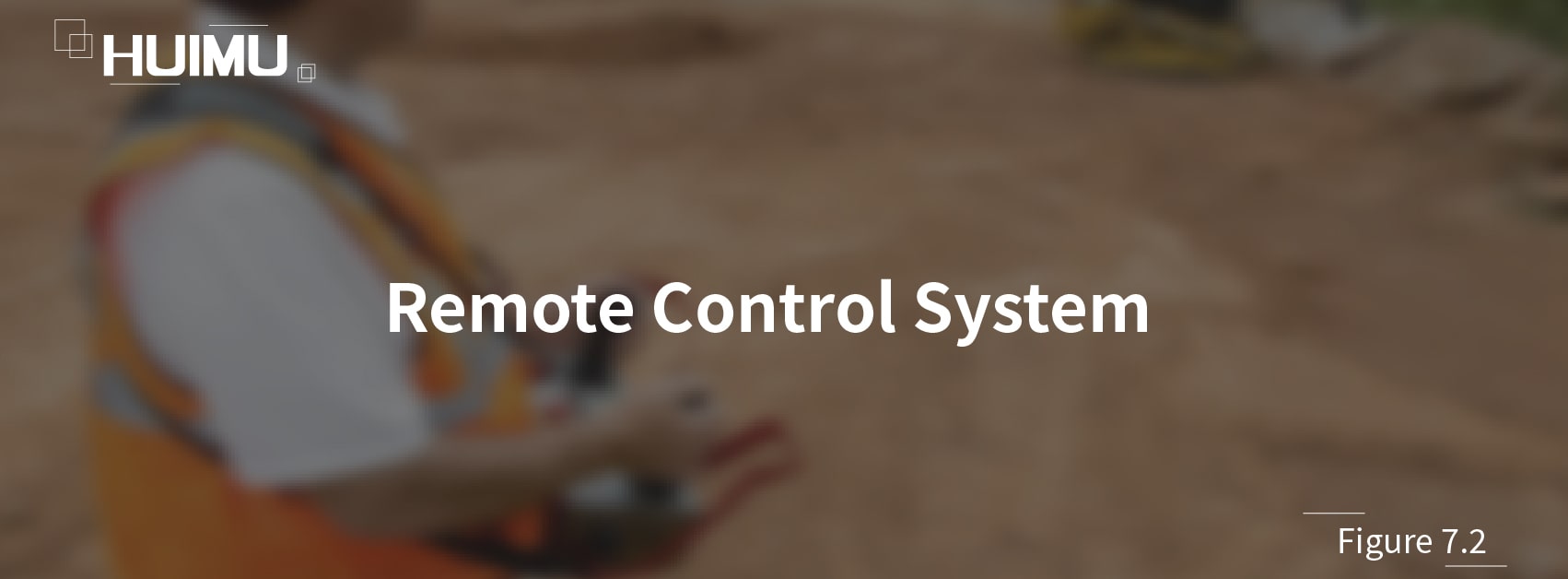
Remote control systems typically require small current signals to control high power equipment, such as electric motors, pulse valves, and other machinery. As an electronic switching element without mechanical contacts, solid state relays are widely used in remote control systems with excellent advantages: flexible control, high reliability, high durability, no spark, no noise, fast switching, high operating frequency, strong anti-interference ability, etc.
Computer Numerical Control Machinery:
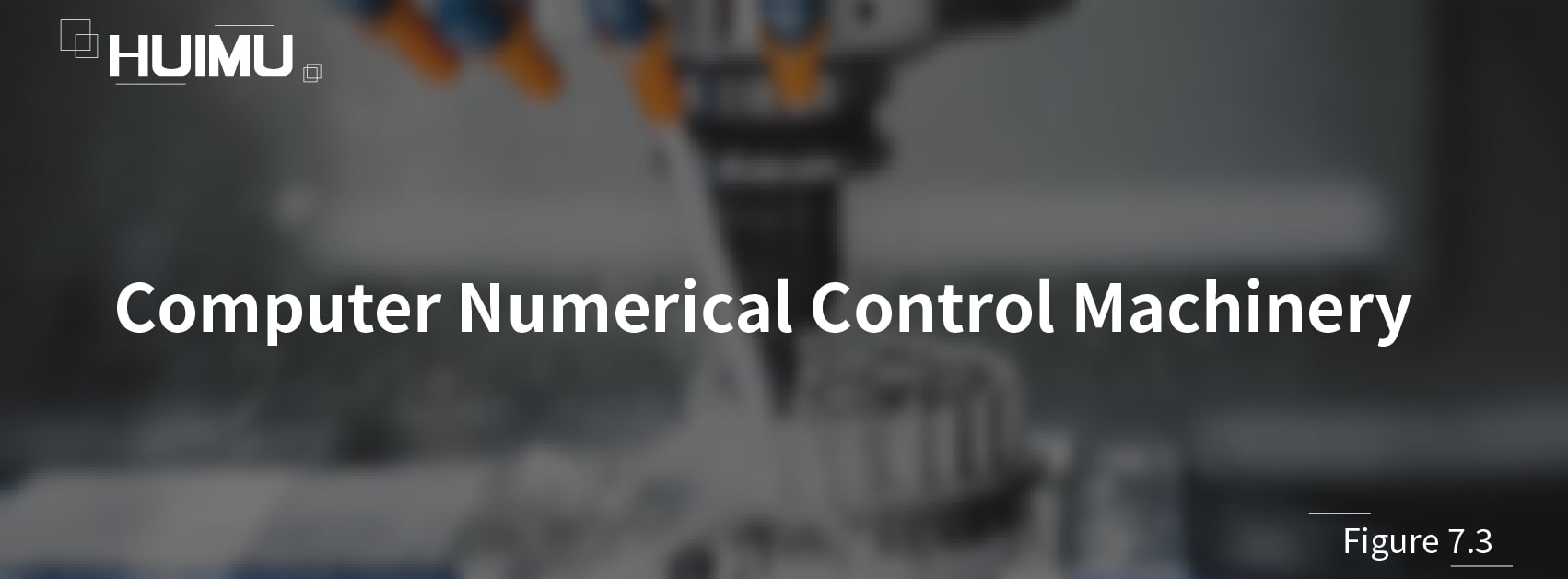
Many traditional mechanical relays in Computer Numerical Control machinery (CNC machine) are gradually being replaced by the solid-state relays. On account of the excellent durability and high sensitivity abilities, the solid state relays are applied to ensure the high precision and high quality of CNC machining. In the servo system of CNC machine, the solid state relay can receive the control signal continuously, and control the processing machine accurately.
Heating/Cooling Equipment:
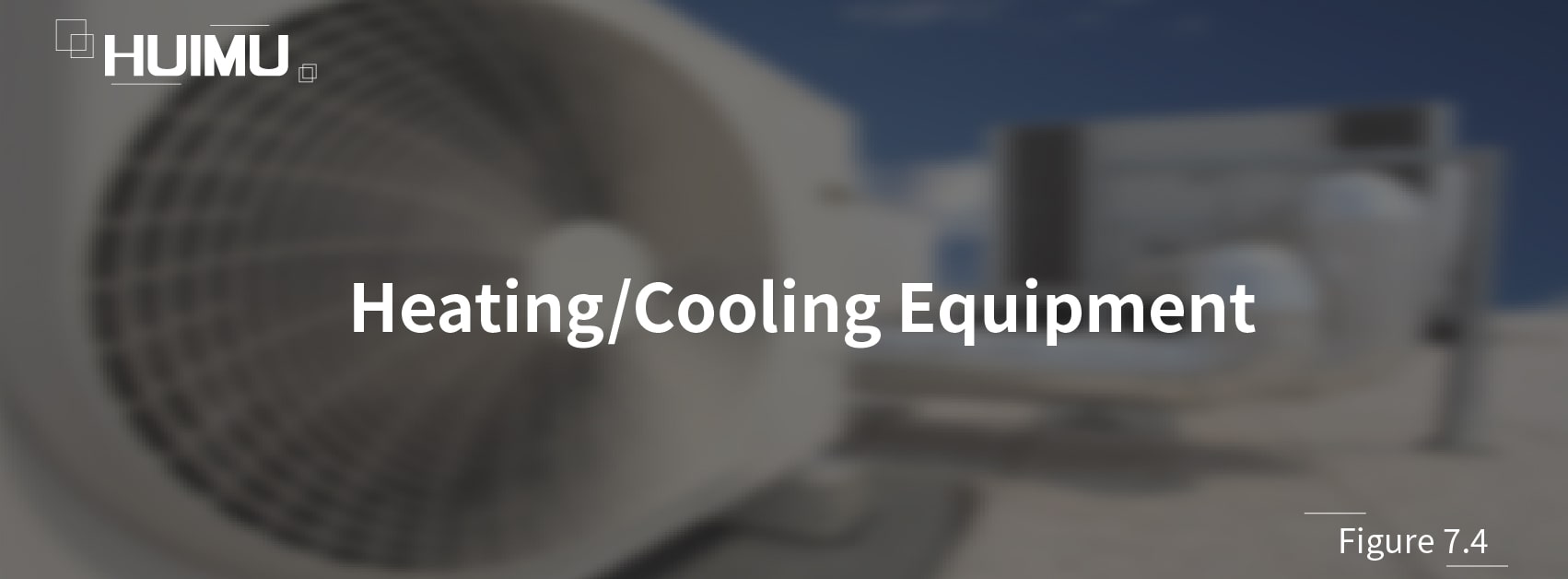
Normally, there are three ways to control the heating /cooling equipment: solid state relay (SSR), thyristor module (SCR module), and AC contactor. Currently, solid state relays and SCR modules are very common in cooling/heating equipment, but in contrast, SCR modules are not cost effective, so solid state relays are most common in heating/cooling equipment, such as electric ovens, coffee machines, vending machines, griddles, Fryers, air-conditioner, refrigerator and etc. The solid-state relays also perform well in temperature control equipment. The timer control SSR, the microcontroller control SSR and PID control SSR (proportional–integral–derivative controller) are used in the temperature control device to maintain temperature stability of the device, like HVAC (Heating, Ventilation, and Air Conditioning).
Medical Devices:
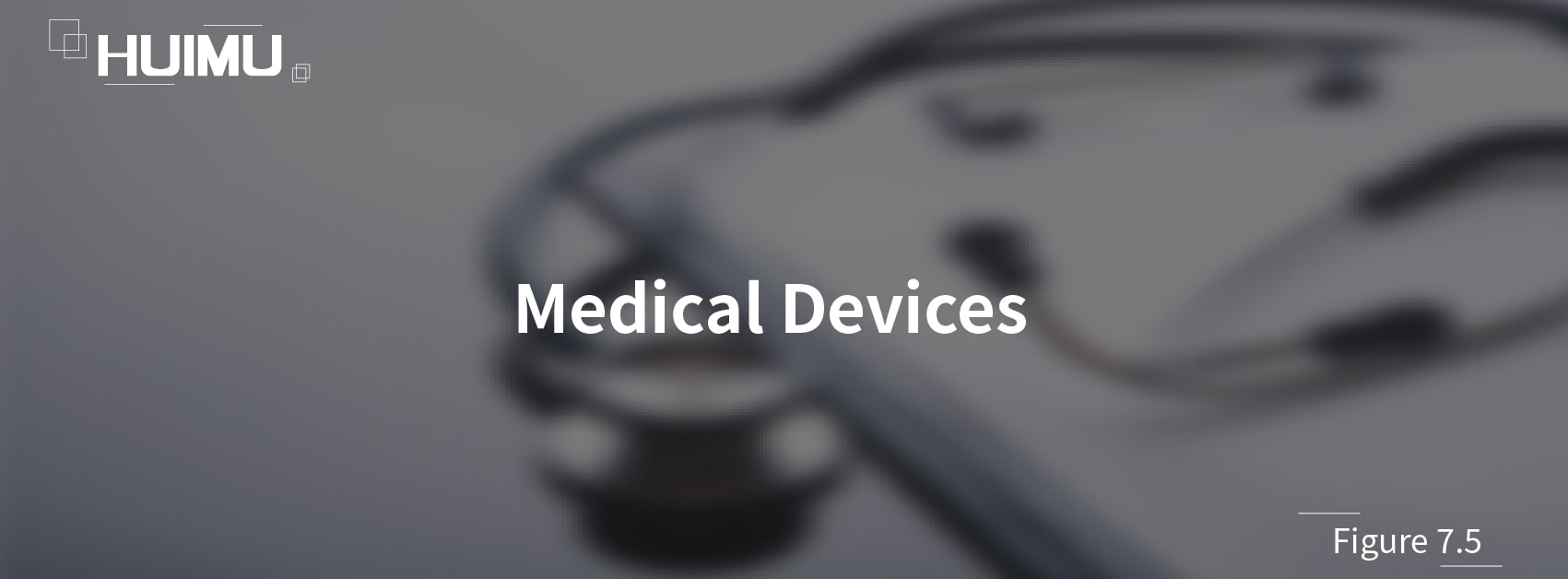
In the field of medical equipment, the equipment has strict requirements of operating frequency and precise operations, so the components of medical equipment should have nice performance (high precision, durability, etc.). Solid state relays can meet these demands of most medical devices, for example, the infrared radiation devices have a huge thermal inertia, but by connecting the solid-state relays to the radiation plate, it becomes very easy to control the temperature of the infrared radiation device through the solid state relays.
Electric Vehicles:
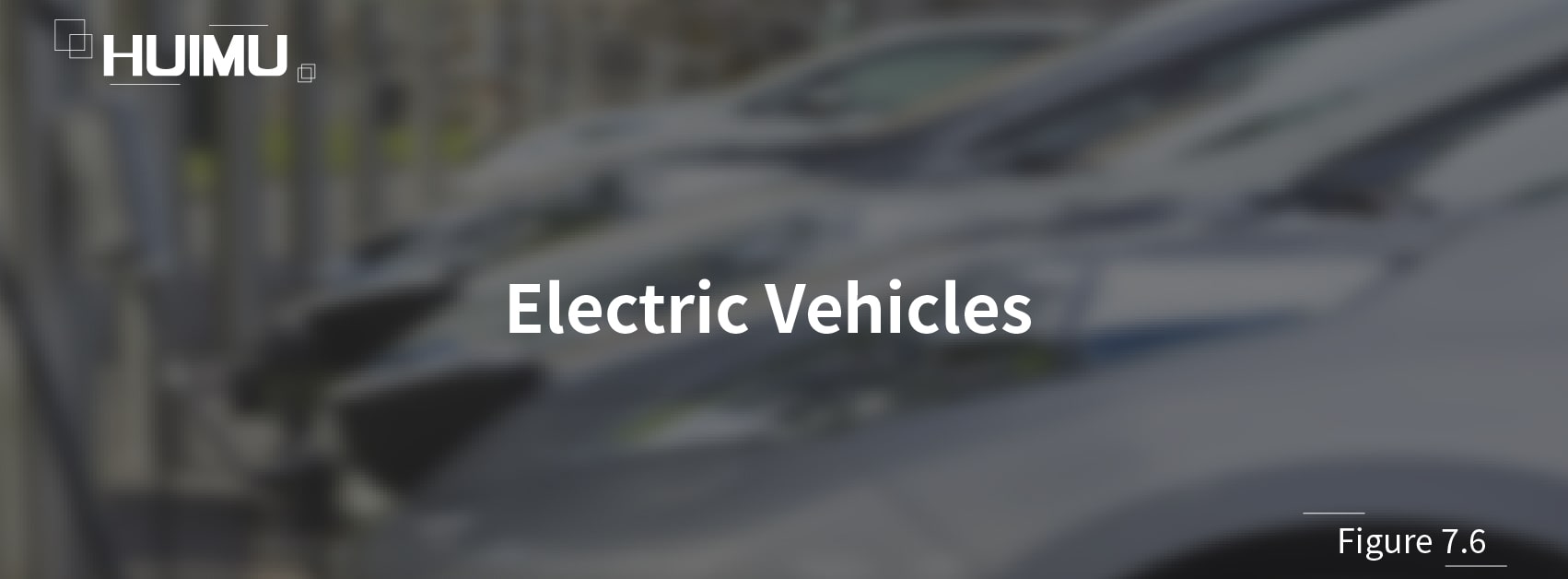
Solid state relays are widely applied in the field of electric vehicles. For example, the explosion-proof solid-state relays are used in the fuel-cell vehicles (hydrogen fuel cells) to avoid electric arcs and incorrect operation during vibration. As well as, each high-voltage power unit is protected by the combination of multiple solid-state relays, fuses and filter capacitors.
Chemical and Mining Industry:
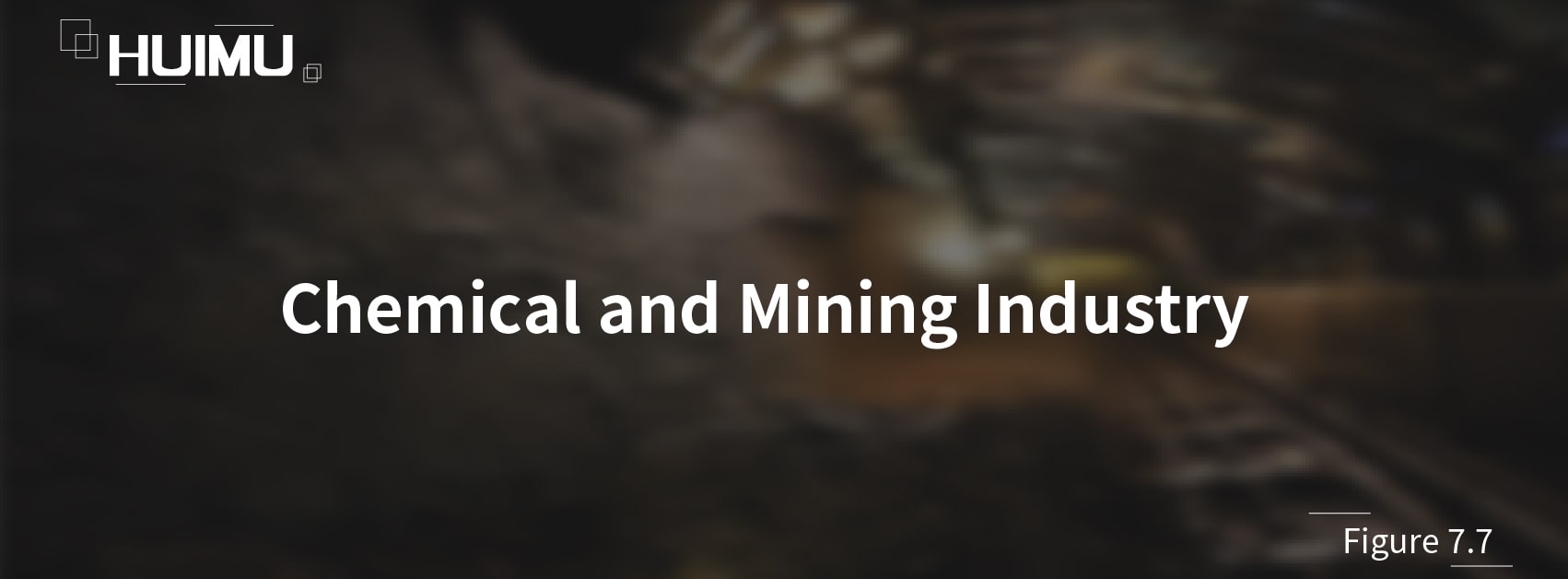
Considering the complex working conditions and special requirements (the explosion-proof, moisture-proof and anti-corrosion abilities) of the chemical and mining industry, the traditional mechanical relays cannot meet such requirements, therefore lots of solid-state relays are used to the intermediate controllers of the major mechanical equipment, such as the solid state relays equipped in large coal mining elevators.
Computer Control System:
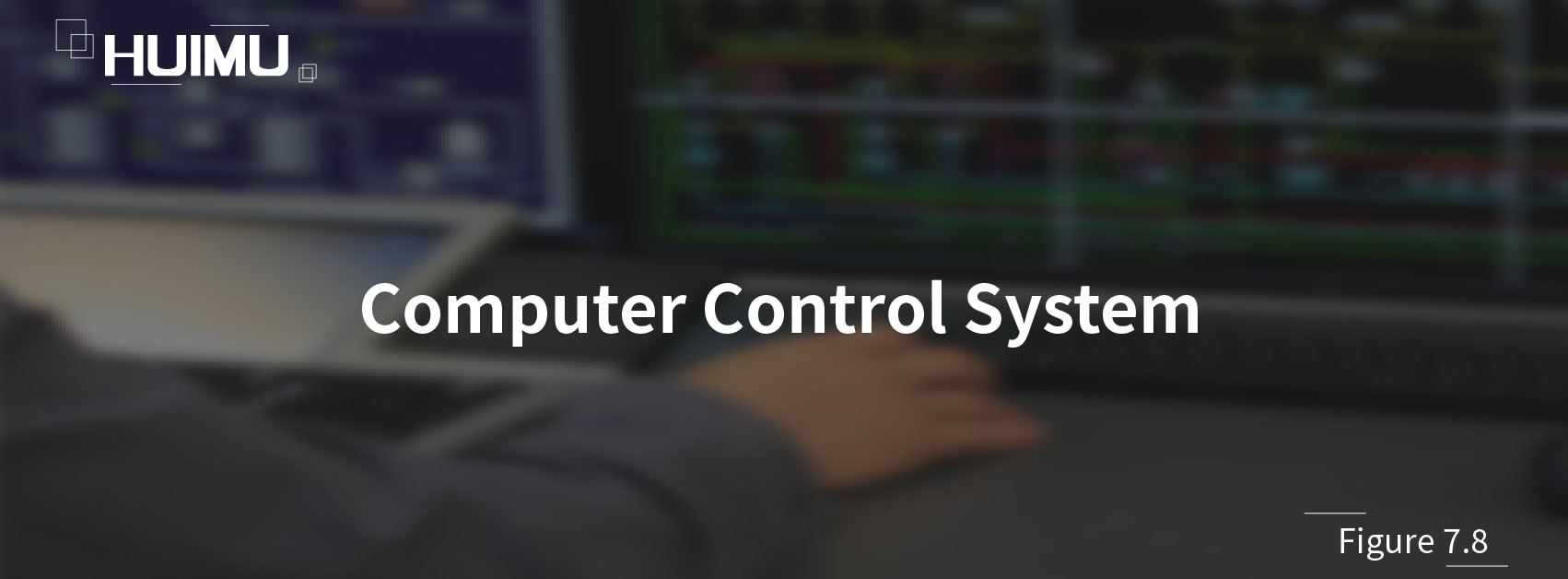
The computer control system (including the computer peripheral devices) have high requirements of relays, but types various of solid-state relays can help the computer devices control assorted power units to drive the large mechanical automation equipment, or hydraulic and pneumatic equipment, because solid state relays have the characteristics: zeroing-crossing, nice electromagnetic compatibility, high sensitivity, fast switching speed, low level control signals, compatible with logic circuit (TTL, CMOS, DTL, HTL) and even can be directly connected to the micro-computer control device, and so on.
More Applications:
Industrial Devices --Industrial Processing, CNC Machine, Automated Assembly Line ...
Kitchen/Home Appliances -- Kitchen Appliances, Home Appliances ...
Electric Motor -- DC Motor, AC Motor, Reversible Motor ...
Automatic Control System -- Programmable Controller, Electric Control Cabinet ...
Office Equipment -- Printer, Shredder ...
Battery Manage System -- Backup Power Supply, Charging Pile, New Energy ...
Welding/Cutting Machines -- Spot Welding Machine, Electric Welding Machine, Plasma Cutting Machine ...
Lighting Control System -- Stage Lighting, Smart Lighting, Traffic Lighting ...
§8. How to select the Solid State Relays
The following are options to consider when selecting the appropriate solid-state relays based on the actual requirements:
1) Load Voltage - AC or DC
2) Load Current - Maximum Current and Minimum Current
3) Load Type - resistive, inductive or capacitive
4) Input Control Signal - AC or DC
5) Mounting Method - PCB, Panel or DIN rail mounting
6) Ambient Temperature - for calculating the Derating Factor and the size of the heat sink
7) International Certification – Underwriter Laboratories (UL), Canadian Standards Association (CSA), British Approvals Board of Telecommunications (BABT), Verband Deutscher Elektrotechniker (VDE), Technischen Uberwachungs Vereine (TUV), Conformite Europeene (CE) or other.
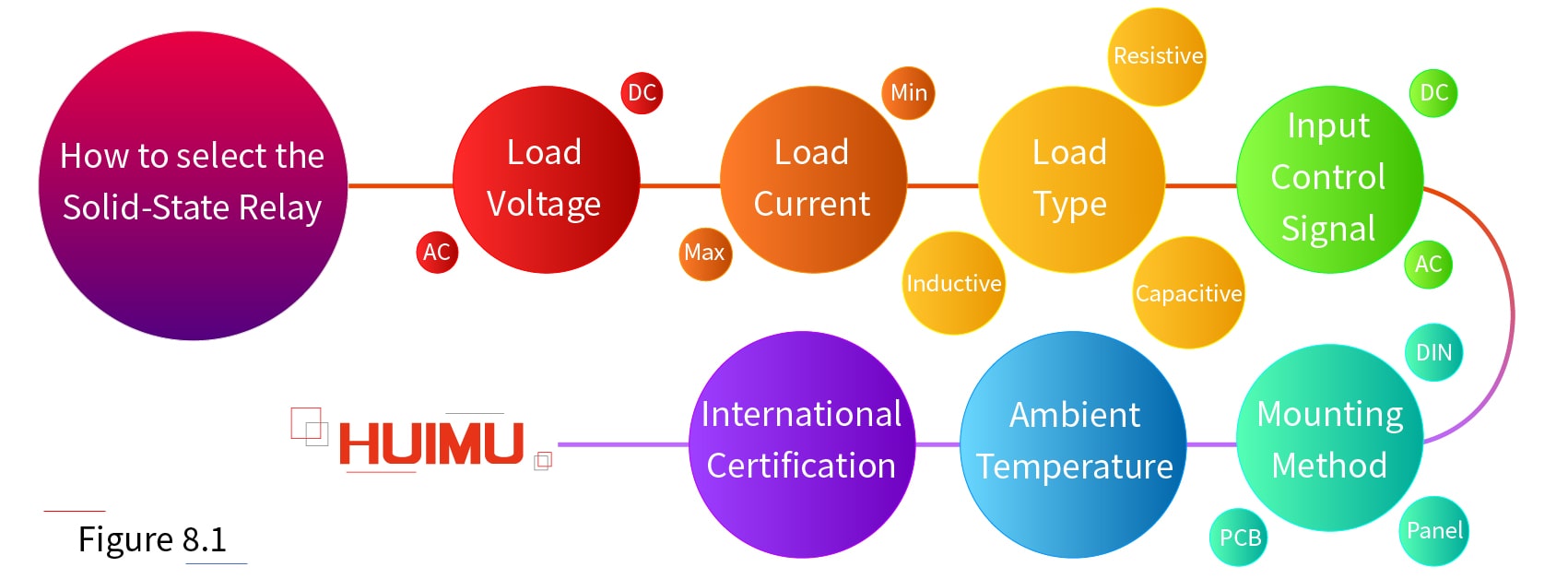
Load Voltage:
The first consideration is whether the load voltage is AC or DC to determine whether AC-SSR or DC-SSR is selected. Secondly, the voltage of the load power supply should be considered which cannot be larger than the output rating voltage, and less than the minimum voltage of the solid-state relay. Then consider the magnitude of the load voltage and the transient voltage. The load voltage refers to the steady-state voltage applied to the SSR switch output terminal, and the transient voltage refers to the maximum voltage that the output terminals of the SSR relays can withstand. When the AC inductive load, single-phase motor load or three-phase motor load is switched or energized, the voltage at the SSR switch output may be twice the peak voltage of the power supply, and this voltage cannot be greater than the transient voltage of the SSR to prevent the excessive shock voltage from damaging the electronic switch. Therefore, when selecting the SSR, it is best to leave a margin for the output voltage, and select the SSR relay with RC Circuit to protect the solid-state relay and optimize dv / dt.
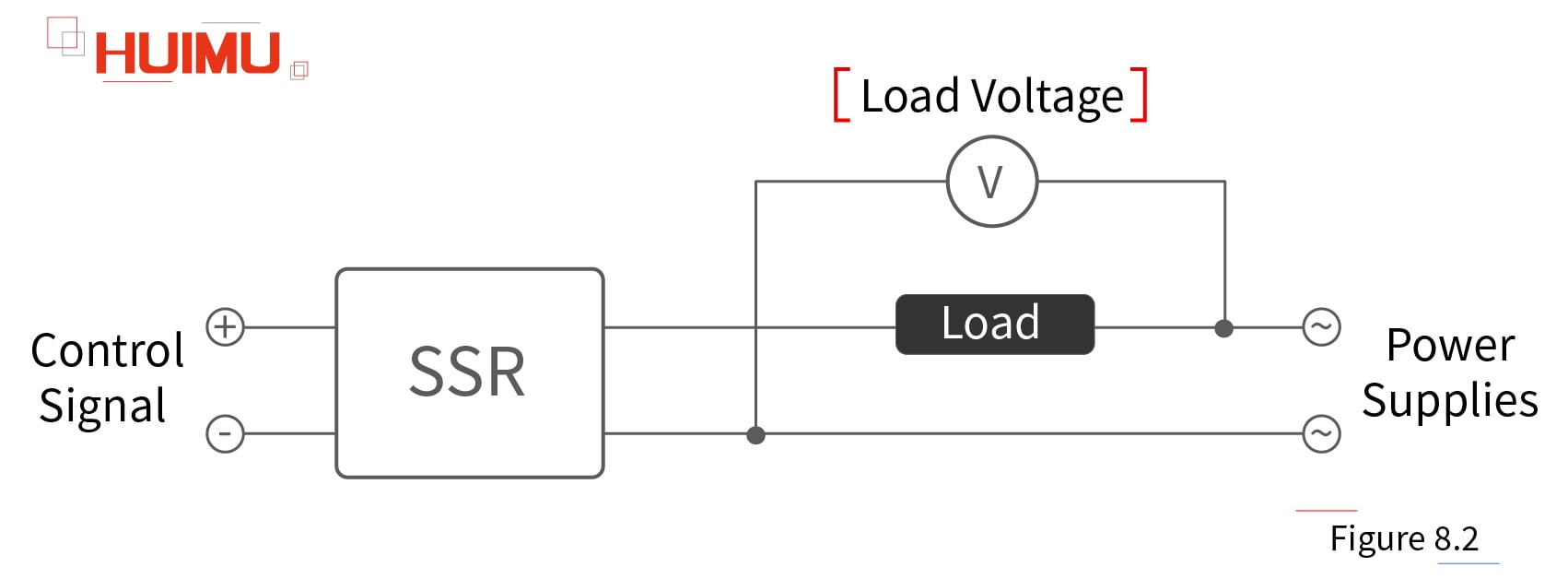
RC Circuit:
RC circuit, also known as RC filter, RC snubber, or RC network, is a circuit consisting of the resistor and the capacitor. It is recommended to select solid state relays with a varistor absorption circuit and an RC snubber circuit. The RC circuit blocks certain frequencies from passing and allows other frequency signals to pass to filter out the interfering signals. Moreover, the RC circuit can also be used to reduce the rise rate of the output voltage (dv/dt), to absorb the surge voltage, suppress excessive transient voltage / current, and prevent the solid-state relay from being broken due to overvoltage.
Load Current:
The output current value of the solid state relay is the steady-state current flowing through the output terminals of SSR, which is usually equal
to the current of the load connected to the SSR output terminal. Since the switching elements of the SSR switches are very sensitive to temperature, and the overcurrent can generate a high amount of heat, so the overload capability of the SSR
is weak. Therefore, the output current of the SSR relay shall not exceed its rated output current, and the surge current shall not exceed the overload capacity, especially for inductive/capacitive loads that are prone to generate surge currents,
as well as the inrush current generated by the power supply itself.
The output current requires a margin to avoid excessive inrush currents that reduce the life of the solid-state
relay. For general resistive loads, the rated effective operating current value can be selected based on 60% of the nominal value. Besides, the fast fuse and the air switch could be considered to protect the output loop, or add an RC sink loop
and a varistor (MOV) to the output of the relay. The selection specification of varistor is to select 500V~600V MOV for 220VAC SSR, and 800V~900V MOV for 380VAC SSR.
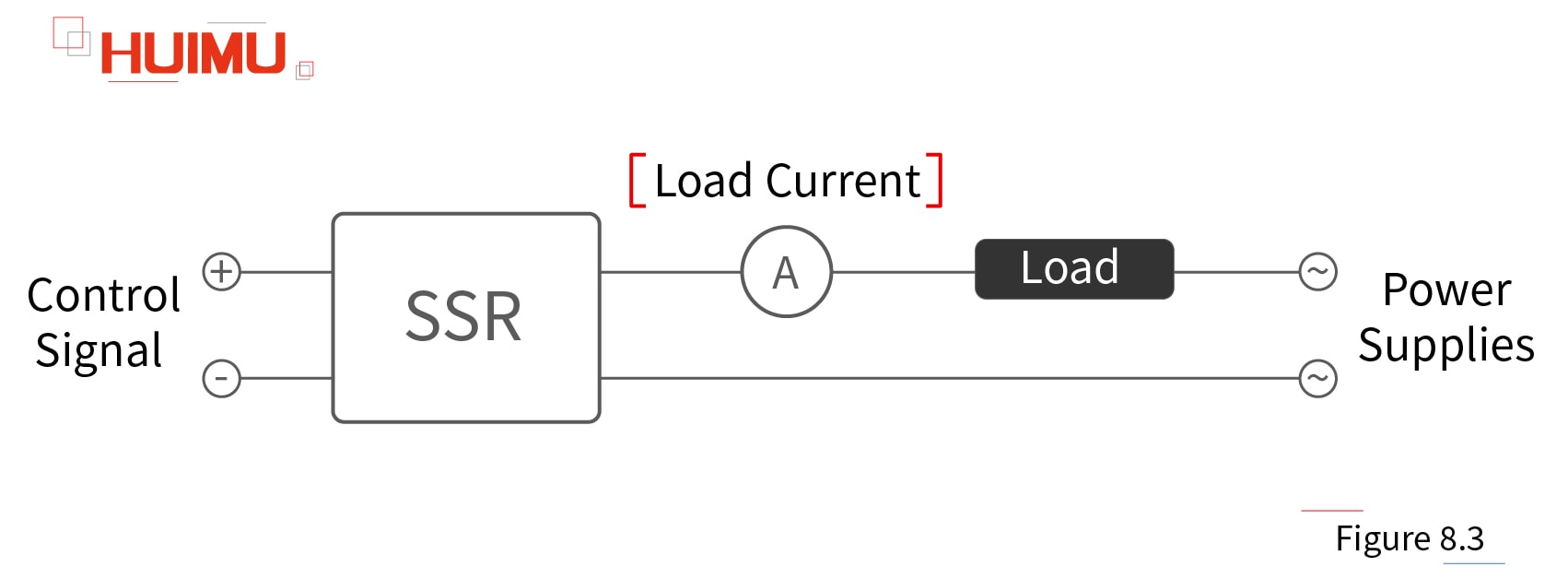
Inrush Current:
Almost all the controlled loads will generate large inrush currents at the moment of turn-on. For example:
1) The electric heating devices, like the incandescent lamps, and the electric furnaces, etc. They are purely resistive loads with a positive stability coefficient, but the resistance is small at a low temperature, so the current at startup will exceed several times the steady state current.
2) Some types of lamps have low impedance when burned off.
3) When the motor is turned on, rotor locked, and turned-off, it will generate large inrush current and voltage. The locked-rotor is a situation in which the motor still outputs torque when the speed is 0 rpm, at the meantime, the power factor of the motor will be extremely low, and the current can be up to 7 times of the rated current.
4) When the intermediate relay or solenoid valve is not closed reliably and bounce, it will also generate large inrush current.
5) When the capacitor bank or capacitor power supply are switched, there will cause a similar short circuit condition, and generate very large current.
6) When the capacitor commutated type motor is reversing, the capacitor voltage and the supply voltage are superimposed on output terminal of the SSR, and SSR will withstand a surge voltage twice the supply voltage.
Excessive inrush current can damage the semiconductor switches inside the SSR. Therefore, when selecting a relay, the surge characteristics of the controlled load should be analyzed first, so that the relay can withstand the inrush current while ensuring steady-state operation. The rated current of solid state relay should be selected according to the derating factor in actual requirements. And if the selected relay needs to work in a place with frequent operation, long life and high reliability, the rated current should be divided by 0.6 based on the known derating factor, to ensure the reliability of operation. Additionally, the resistor or inductor can be connected in series to the output loop to further limit the current.
Attention: Please do not use the SSR surge current value as the basis for selecting the load starting current. Because the SSR relay surge current value is based on the surge current of electronic switch with the precondition of half (or one) power supply cycle,
that is 10ms or 20ms.
Load Type:
The loads can be divided into three types based on the electrical impedance: Resistive Load Type (or Pure Resistive Load), Inductive Load Type and Capacitive Load Type. There is no pure inductive load and pure capacitive load in the usual electrical appliances, because these two type loads don not do active power. In the series-parallel circuit, if the capacitive reactance is larger than the inductive reactance, the circuit is capacitive load; and vice versa.
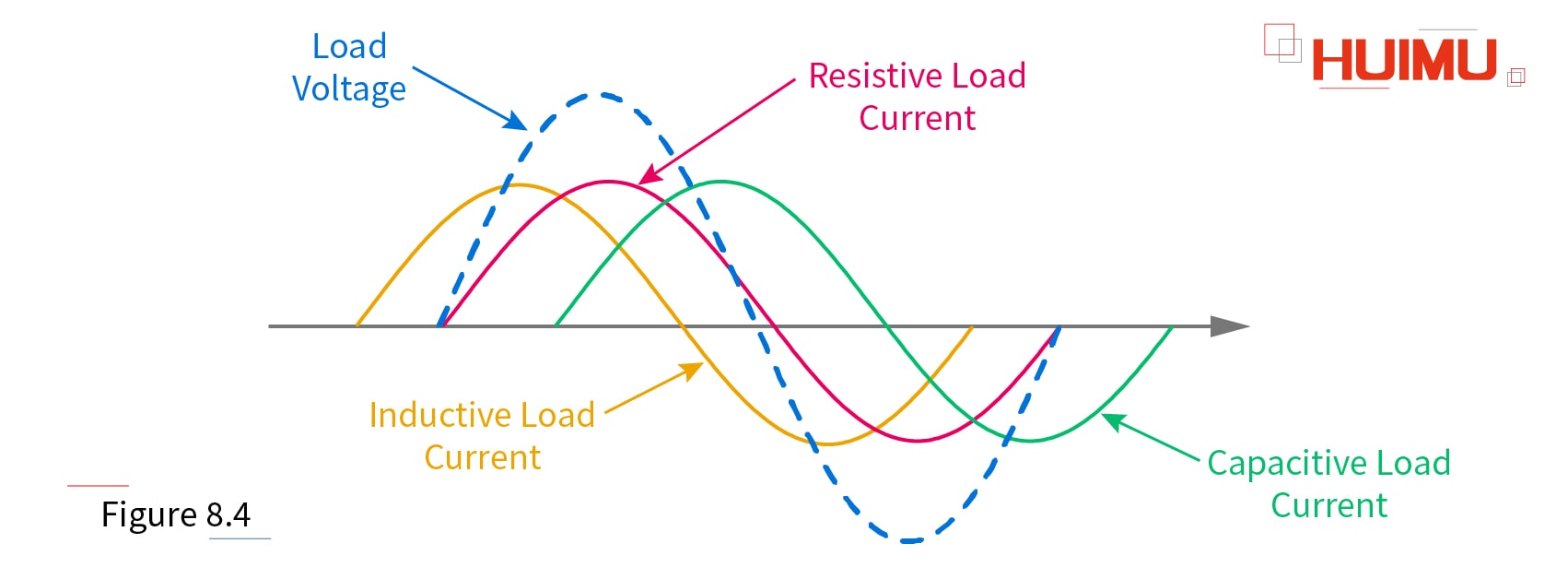
Resistive Load:
In a nutshell, a load that operates only by then resistor-type components is called the resistive load. However, some loads have low resistance at low temperatures,
which results in a larger startup current. For example, when the electric furnace is just turned on, the current is 1.3-1.4 times larger than the stable current; when the incandescent lamp is turned on, the current is 10 times larger than the steady current.
Q1: What are the characteristics of the resistive load (when working)?
A1: In the DC circuit, the relationship between current and voltage is in accordance with the fundamental ohm's law, I=U/R; in an AC
circuit, the current phase is the same as the phase of the voltage (compared to the power supply).
Q2: Which are resistive loads?
A2: Heating device that is heated by electric resistance (like resistance furnace, oven, electric water heater, hot oil, etc.), and lamps that rely on resistance wire to emit light (like iodine tungsten lamp, incandescent lamp, etc.).
Inductive Load:
Generally speaking, the inductive load is the load that applies the principle of electromagnetic induction (with inductance parameters), such as high-power
electrical products (like refrigerators, air conditioners, etc.). The inductive load will increase the power factor of the circuit, and the current through the inductive load cannot abrupt change. At startup, the inductive
load requires a much larger starting current (approximately 3-7 times) than the current required to maintain normal operation. For example, the starting current of an asynchronous motor is 5-7 times the rated value, and the starting current of the DC motor is slightly larger than the starting current of
the AC motor; some metal-halide lamps have a turn-on time of up to 10 minutes, and their pulse currents up to 100 times steady state current.
Furthermore,
when the power is turned on or off, the inductive load will produce a counter-electromotive force (usually 1-2 times the supply voltage), and the counter electromotive force(abbreviated counter EMF or simply CEMF) will be superimposed with the power supply voltage, and the resulting voltage is up to three times the supply voltage. So, when the load type is an inductive load, the output terminal of solid-state relay
should connect a varistor with a withstand voltage of 1.6-1.9 times the load voltage. The counter EMF is an indefinite value that varies with L and di/dt, and if
the current rate of change (di / dt) is too high, the SSR will be damaged. In practical applications, CEMF can be reduced by series inductance L, and the magnitude of the L inductance depends on the size and cost.
Q3: What are the characteristics
of the inductive load (when working)?
A3: Inductive loads are lagging (current lags voltage). In the DC circuit, the inductive load allows current to flow through and energy to be stored in the inductor, and the current lags behind the voltage.
In the AC circuit, the current phase lags behind the voltage phase (compared to the power supply), and the phase can lag a quarter cycle (or 90 degrees) at the maximum.
Q4: Which are inductive loads?
A4: Lamps that rely on energized
gas to emit light (like daylight lamps, high-pressure sodium lamps or HPS lamps, mercury lamps, metal-halide lamps, etc.), and
high-power electrical equipment (like motor-based equipment, compressors, relays, etc.).
Capacitive Load:
Generally, a load with a capacitance parameter is called the capacitive load, and the capacitive load will reduce the power factor of the circuit. During charging or discharging, the capacitive load is equivalent to a short circuit because the voltage across the capacitor cannot be changed abruptly.
Q5: What are the characteristics of the inductive load (when working)?
A5: Capacitive loads are leading (current leads voltage). In the DC circuits, capacitive loads prevent current from flowing, but can store energy. In the AC circuits, the current phase leads the voltage phase (compared to the power supply),
and the phase can lead a quarter cycle (or 90 degrees) at the maximum.
Q6: Which are inductive loads?
A6: Device with a capacitor, such as a compensation capacitor. And power control devices such as switching power supplies, IT equipment and etc.
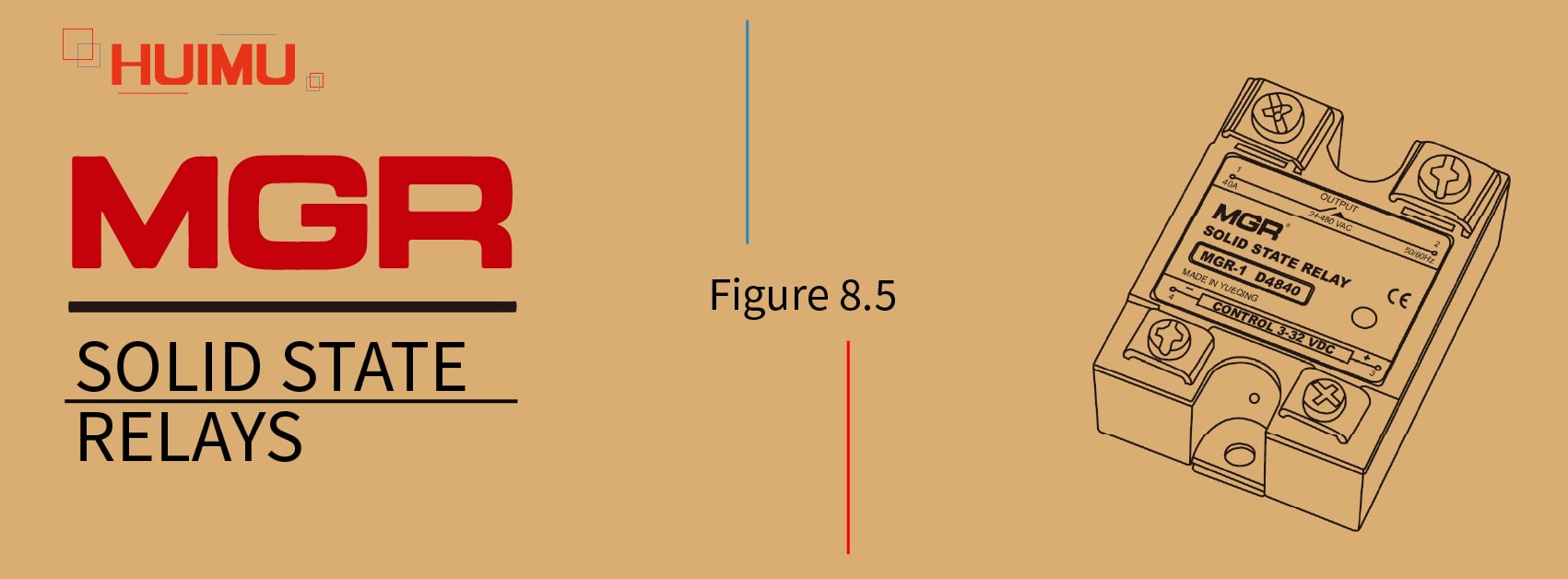
How to choose Solid-State Relay according to load type
1) For inductive and capacitive loads, a solid-state relay with a higher dv/dt is recommended, if there is a biggish dv/dt (voltage exponential rise rate) applied to the relay’s output terminal during the AC solid state relay turning on/off.
2) For AC resistive loads and most AC inductive loads, zero-crossing relays are available to extend the life of load and relay, and reduce their own RF interference.
3) As a phase output controller, a random type solid state relay should be used.
* Power Factor:
In electrical engineering, the power factor of an AC power system is defined as the ratio of the real power flowing to the load to the apparent power in the circuit, and is a dimensionless number in the closed interval of -1 to 1. If it is not specified the load power of the general product is the apparent power (includes both active power and reactive power). But the general specification of the inductive load often gives the magnitude of active power. For example, although a fluorescent lamp is labeled 15 to 40 watts (its active power), its ballast consumes approximately 8 watts of power, so 8W should be added to 15~40w to calculate the total power. The inductive portion of the product (i.e. the amount of reactive power) can be calculated from the given power factor.
Input Control Signal:
1) Input Control Voltage: the input control voltage has a wide range of 3~32V.
2) Input Control Current: the input current of DC SSRs and AC single-phase SSRs is generally around 10mA, and the input current of AC three-phase SSRs is generally around 30mA, which also can be customized to be less than 15mA.
3) Control Frequency: the control operating frequency of AC solid state relays generally does not exceed 10HZ, and the DC solid state relay control signal period should be greater than five times the sum of the relay's "on time" and "off time".
Mounting Method:
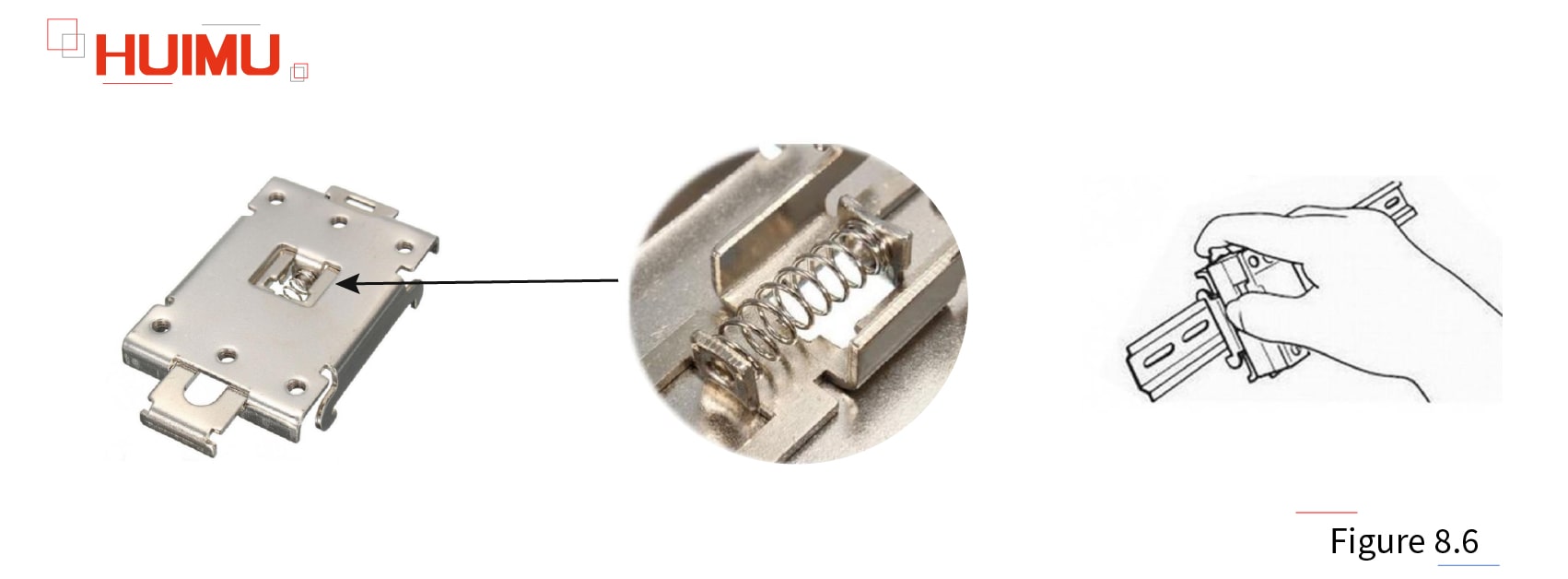
In many cases, the load power will limit whether the SSR is mounted on the PCB, the panel or the DIN rail.
Ambient Temperature:
When the relay is in the on state, it will withstand the dissipated power of P = V (on-state voltage drops) × I (load current), and the load capacity of the SSR is greatly affected by the ambient temperature and its own temperature. If the ambient temperature is too high, the load capacity of the SSR will inevitably decrease accordingly, moreover, the SSR switch may be out of control, or even be permanently damaged. Therefore, it is necessary to set a certain margin according to the actual working environment, and select the appropriate heat sink size to ensure the heat dissipation conditions. For load currents greater than 5A, a heat sink should be installed. For currents above 100A, the heat sink and fan should be equipped for strong cooling. If the SSR relay is operated at high temperatures (40 ° C ~ 80 ° C) for a long time, the load current can be reduced according to the maximum output current and ambient temperature curve provided by the manufacturer to ensure normal operation, and the load current is usually controlled within 1/2 of the rated value.
* Derating Factor:
The table below shows the recommended derating factor for the rated output current of solid-state relays applied on various loads at room temperature (the overload capability and the load surge current have been considered).
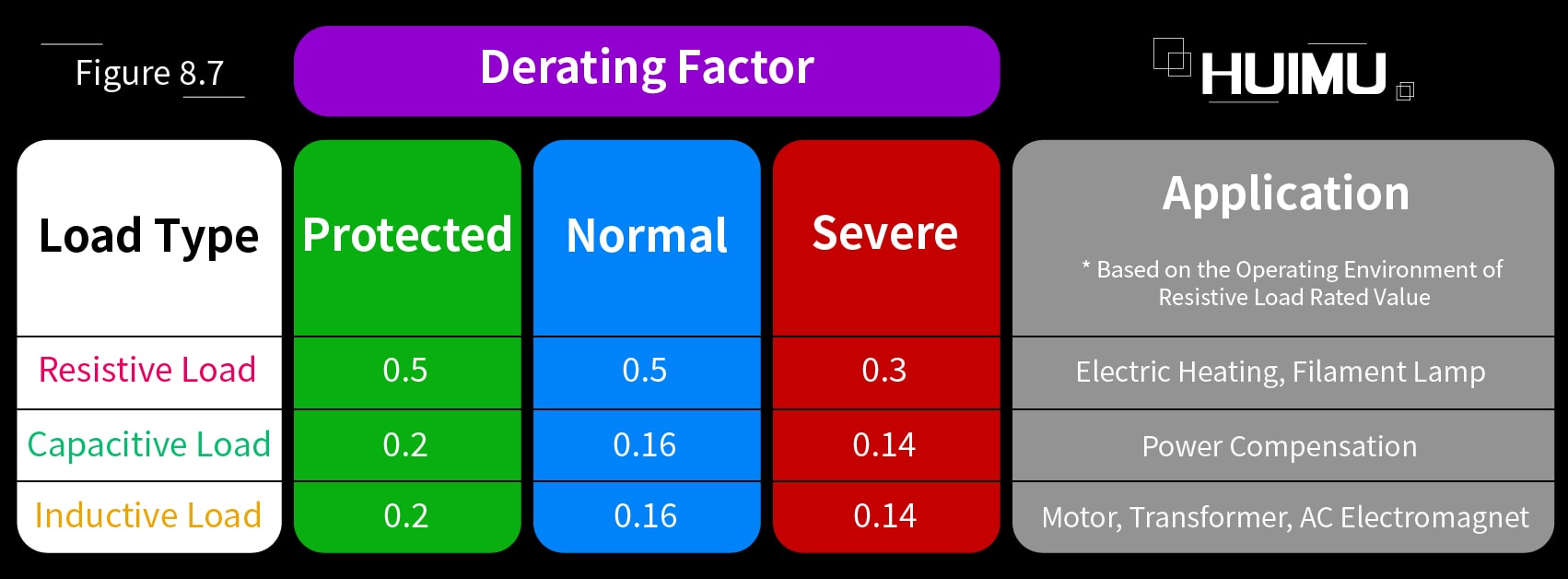
There are two ways to use the derating factor:
1) The rated current value of the solid state relay can be selected according to the derating factor of different environments and different load types. The rated current of the SSR relay is equal to the continuous current value of the load divided by the derating factor.
2) If the solid-state relay has been selected and the load type or environment changes, the load current should be adjusted based on the load curve and the derating factor in certain environment. The adjusted current multiplied by the derating factor must be lower than the rated value of the solid state relay.
In addition, when SSRs are run in applications that require more frequent operation, longer life, and more stable reliability performance, the derating factor needs to be further multiplied by 0.6 based on the data in the table. However, the load current should not be lower than the minimum output current of the solid state relay, otherwise the relay will not be switched on or the output state will be abnormal.
§9. Attentions when using or installing Solid State Relays
1) The actual application conditions of the product must fully comply with the requirements of the parameters and characteristic curves of solid-state relays.
2) SSR should not be used in applications with a large number of low or high harmonic components (for example, multiple sets of loads at the output of the inverter need to be switched separately). If the solid state relay is used in inverter as an electronic switch, because of the higher harmonics, the solid state relays may not be able to switch reliably, and the RC circuit inside the SSR relays will be exploded due to overheating.
3) The SSR relays should be kept away from strong electromagnetic interference sources and RF interference sources to ensure that the SSR can operate stably and safely, avoiding loss of control.
4) Except for the solid state relay with rated current of 1~5A which can be directly mounted on the printed circuit board, the other solid-state relays should be equipped with appropriate heat sinks. Thermal grease should be applied between the SSR base plate and the heat sink, and screwed tightly to make them close to each other for optimum heat dissipation. Or install a temperature control switch near the SSR relays backplane and the temperature control point is typically set between 75 °C and 80 °C.
5) When the input voltage of the input control signal is too high and exceeds the rated parameter of the SSR, the input resistor can be connected in series to the input circuit to reduce the excess value. Similarly, when the input current is too large, the shunt resistor can be connected in parallel to the input port.
6) The control signal and the load power supply need to be stable, and the fluctuation should not exceed 10%, otherwise the voltage regulation measures should be taken.
7) If using solid state relay to control the primary circuit of the transformer, the influence of the transient voltage of the secondary circuit on the primary circuit should be considered. In addition, since the current is asymmetrical in both directions, the transformer may also generate surge currents caused by saturation. In this case, the oscilloscope can be used to measure the inrush current and voltage that can be caused, so that the appropriate SSR and protection measures can be selected.
8) The output of the solid state relay is not completely isolated, when load power is applied to the output terminals, even if the solid-state relay does not operate, there will be some leakage current at the output terminals, which should be noted when using and designing the circuit. During maintenance, the service personnel must cut off the power supplies before checking the output circuit.
9) When a solid state relay needs to be replaced due to a fault, the SSR relay with the same model or technical parameters is recommended, to match the original application circuit and ensure reliable operation of the system.
§10. Attentions when testing Solid State Relays
1) First the relationship between the output current and the shell temperature (ambient temperature) should be known before testing to avoid permanent damage to the SSR caused by overload, because the rated output current will drop when the case temperature rises or with no radiator.
2) When testing the turn-on and turn-off voltage of DC-SSR, the input voltage cannot remain in the state between on and off for too long, otherwise the power consumption of the output terminal rises sharply and burns out the output switching components.
3) Do not arbitrarily speed up the action rate during the test (usually one period of the input signal should be more than 5 times the sum of the on/off times), otherwise the SSR relay will not work due to the large dynamic-switching-loss, or even the output switching components will be burnt out.
4) The solid state relays cannot achieve complete isolation between the output terminals in the off state, and there will be a certain leakage current at the output terminal. When the dielectric withstand voltage and insulation resistance are tested at a higher voltage, it is prone to electric shock, so the insulation resistance or the withstand voltage must not be tested on the output terminals.
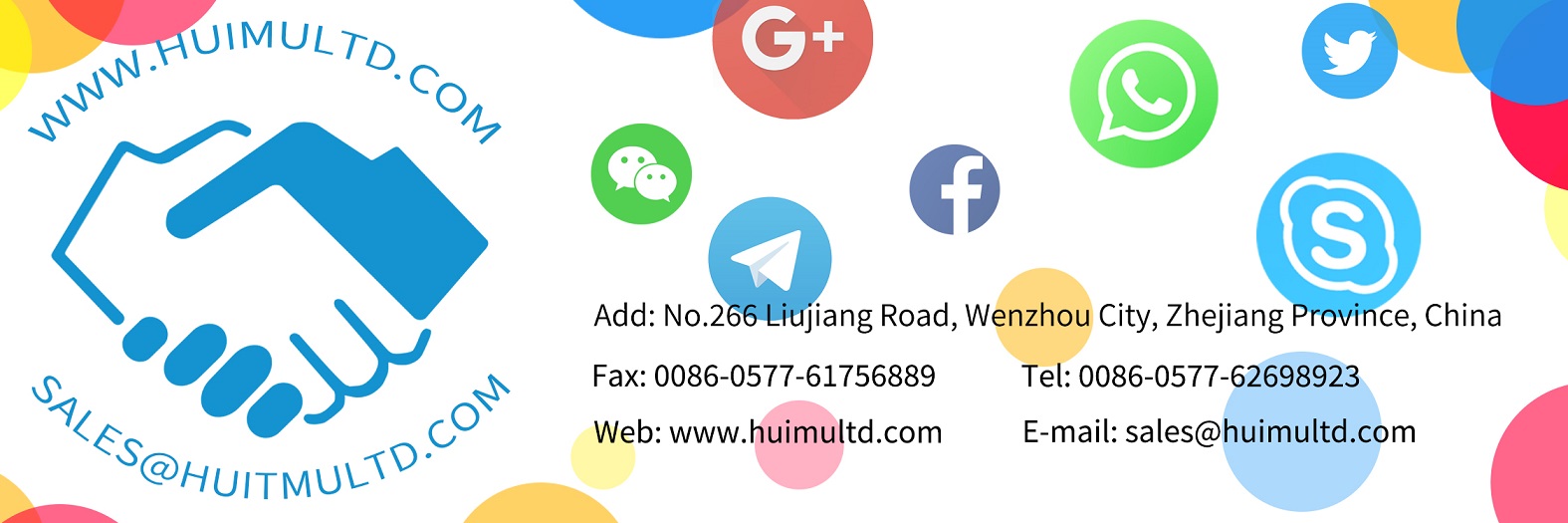
Bitte kontaktieren Sie uns!
Bitte nehmen Sie sich eine Minute Zeit, um dieses Formular auszufüllen, danke!
*Bitte überprüfen Sie den Papierkorb Ihres Postfachs, wenn Sie unsere E-Mail nicht erhalten.