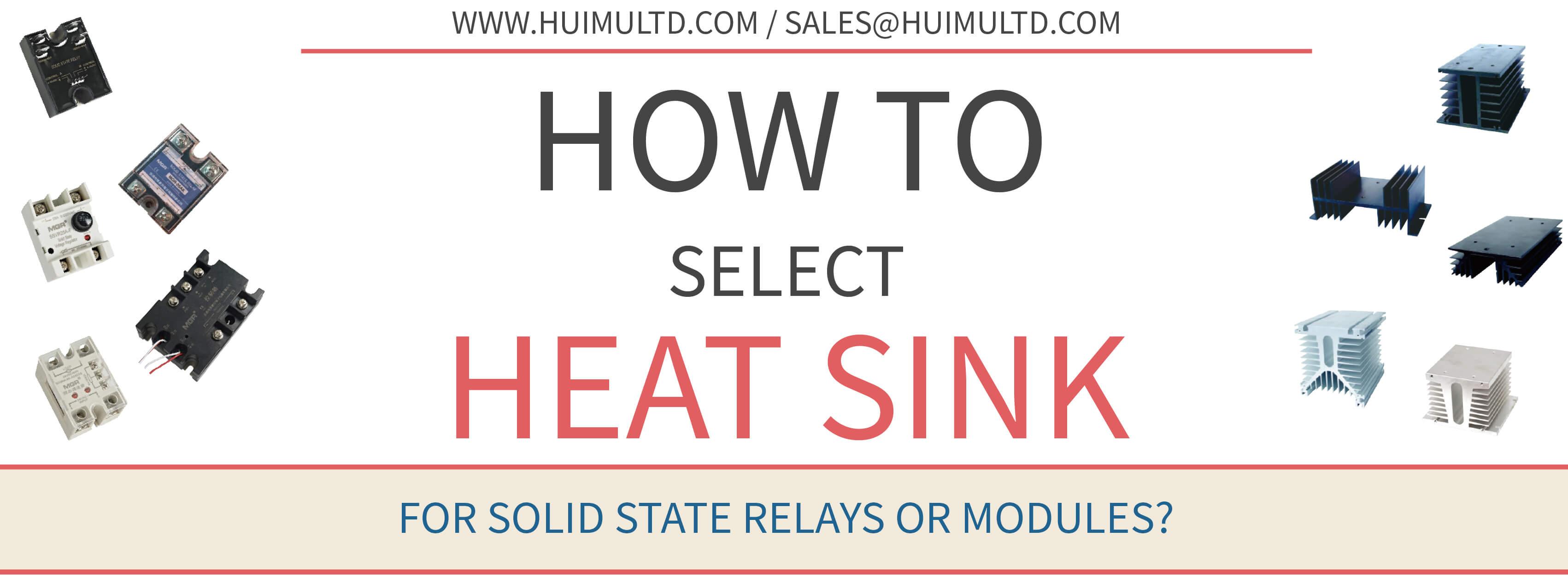
How to select a suitable Heat Sink for Solid State Relays and Solid State Modules?
Solid state relays and modules generate heat when they are in operation. If you want to increase the efficiency and service life of your solid state relays and solid state modules, then you need to choose the right heat sink and radiator. Through this article you will learn how does the heat sink and radiator work? What is the heat calculation formula of the solid state relay and solid state module? How to select a suitable heat sink for solid state relays and solid state modules?
You can quickly navigate to the chapters you are interested in through the Directory below, and the Quick Navigator on the right side of the browser.
CONTENTS
§1. How the Heat Sink and Radiator works? |
§2. How to calculate the Heat? |
§3. How to select Heat Sink and Radiator? |
§1. How the Heat Sink and Radiator works?
The role of the heat sink and radiator is to dissipate the heat generated by the solid state relays and solid state modules to ensure that them work stably and reliable at optimum conditions and not be burned and damaged due to high temperatures. The heat dissipation effect of the heat sink is not only related to its specification (size, shape), but also related to external environmental factors, such as the ambient temperature (season), ventilation conditions (natural cooling or forced cooling, and ventilation volume), and installation density. In addition, it is also necessary to consider whether the volume of the solid state relay or the module itself and the installation space of the heat sink in the equipment matches the specifications of the heat sink.
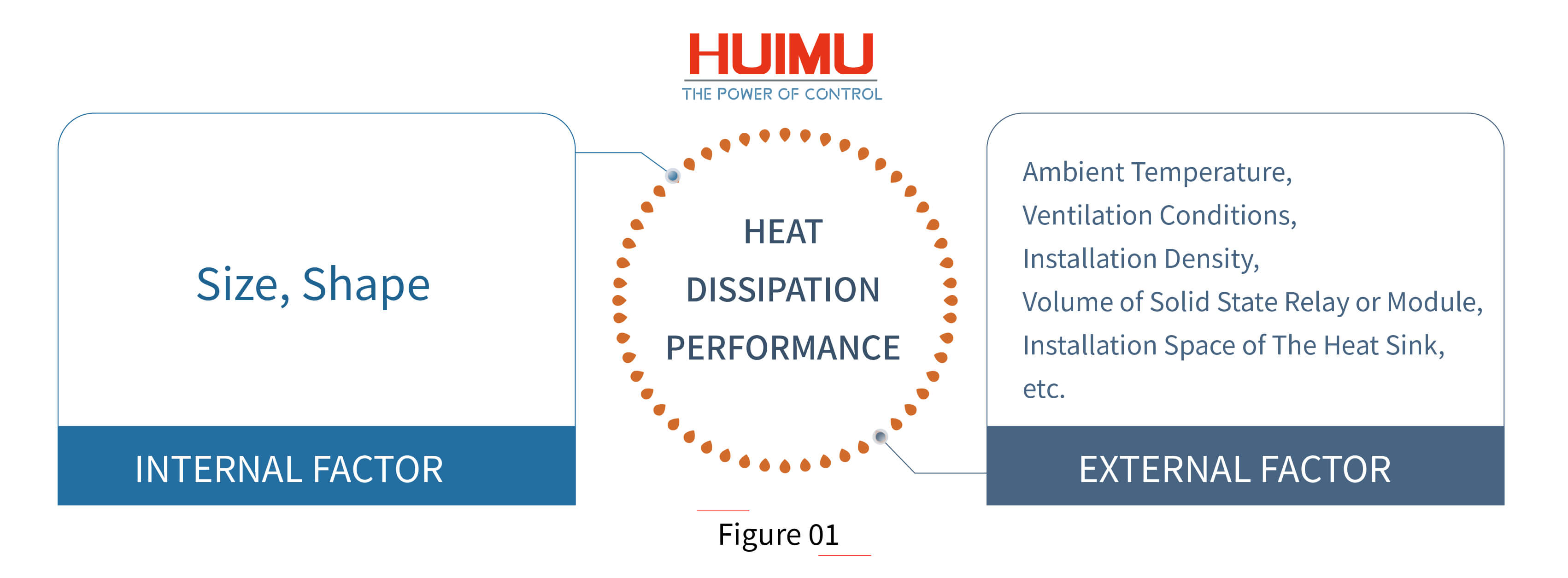
The cooling method of the solid state relay and module can be divided into the air cooling and the water cooling. And the air cooling can be farther divided into the natural cooling (using a heat sink) and the forced cooling (using an air cooled radiator or fan). Normally, if the load current of the solid state relay and module reaches 10A, a heat sink must be equipped. If the load current is 40A or more, an air-cooled radiator or a water-cooled radiator must be installed.
When the solid state module is used for the device with load power greater than 15KW, it is recommended to use a suitable heat sink, applying thermal grease between the heat sink and its backplane, to cool it down by cold air. If the current is below 350A, the solid state module is cooled by forced air cooling. If the current is more than 400A, the cooling method for the solid state module can be either air-cooling or water-cooling.
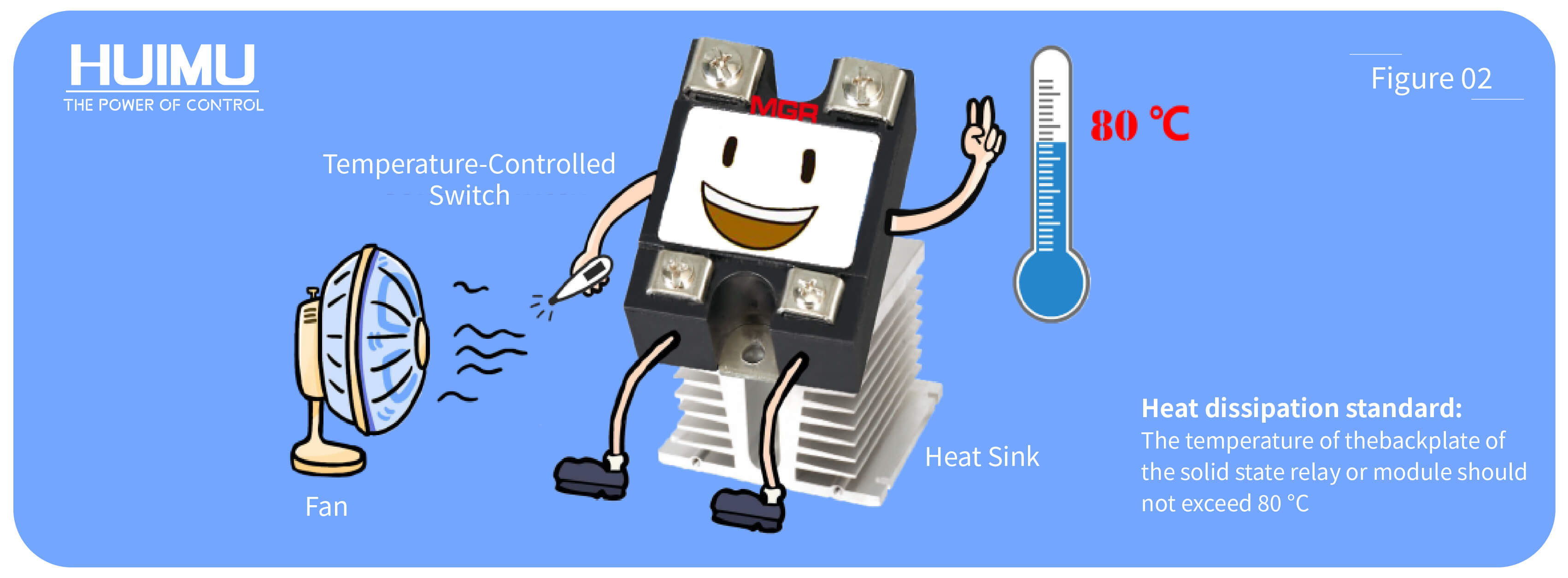
Therefore, in practical applications, we recommend installing a 75° C temperature-controlled switch with a normally closed contact on the mounting surface of the heat sink, that is, within about 20mm of the backplate of the solid-state relay or module, and then connecting the control signal terminal of the solid-state relay or module in series with this normally closed contact. In that case, if this temperature-controlled switch detects that the temperature of the heat sink exceeds 75°C, the normally closed contact will open and cut off the control signal of the solid state relay or module, causing it to shut down immediately. For a three-phase solid-state relay or module, if the actual current on each phase exceeds 50A, it is recommended to install a temperature-controlled switch to protect it to ensure that it will not be damaged by overheating even in relatively harsh working environments.
§2. How to calculate the Heat?
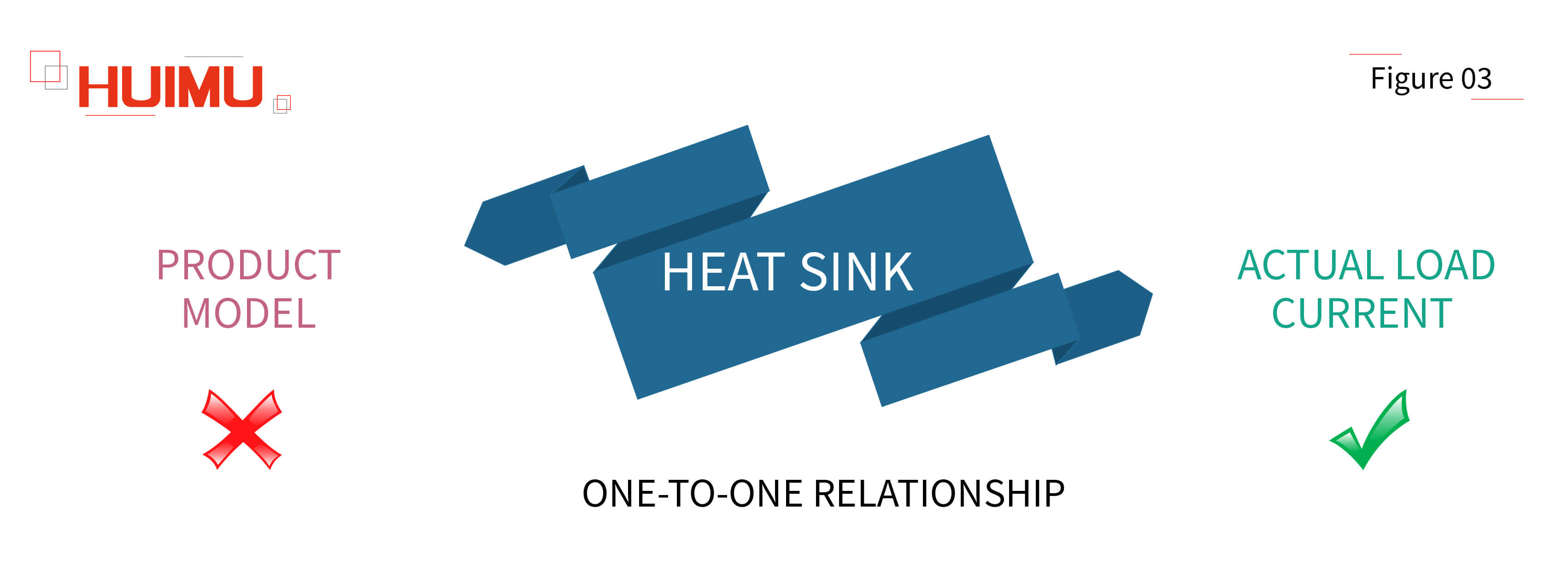
We cannot specify the specification of a heat sink by the model number of a solid state relay or module, but need to know their actual heat generation, which is related to their actual operating power on the one hand, and the specific thermal environment on the other. We can obtain accurate heat data through some heat detection methods or thermodynamic formulas. However, if conditions are limited or you want a simple means, then we can also calculate the heat of a solid state relay or module by using some empirical coefficients.
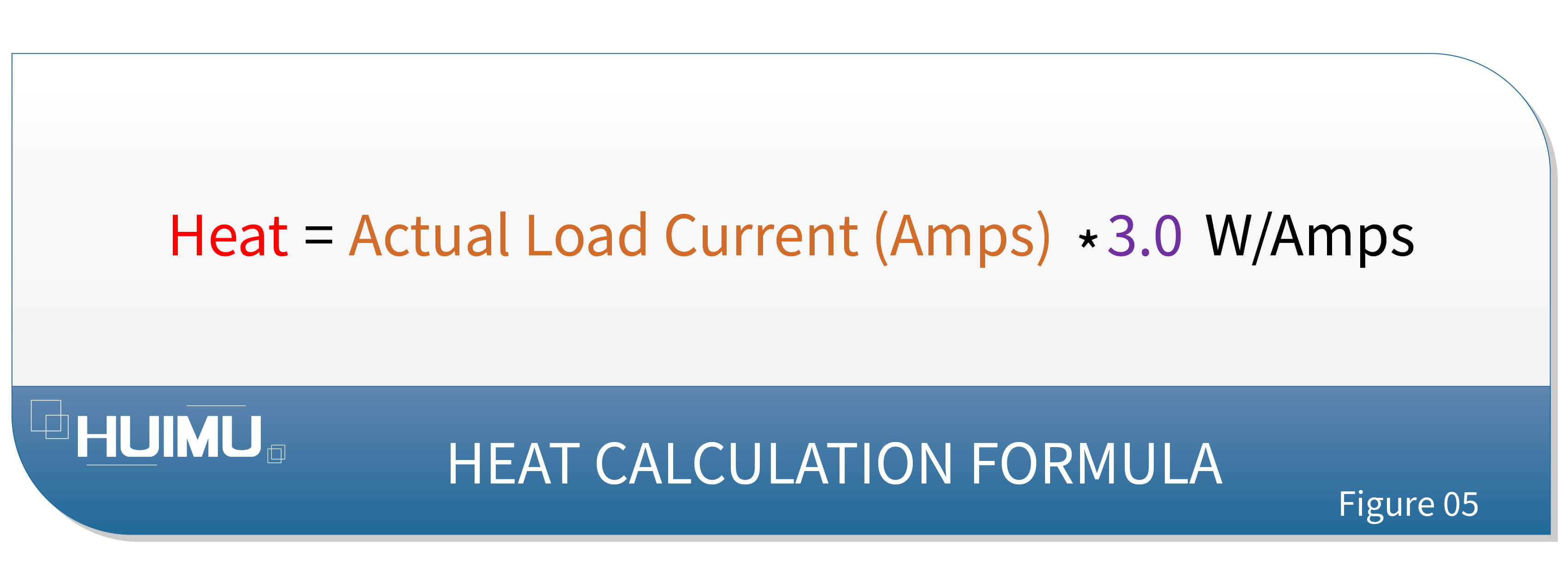
◆ Heat = Actual Load Current (Amps) * 1.5 W/Amps
It is important to note that for single-phase solid state relays, single-phase AC regulator modules, and R-series solid state regulators, if we know their actual load current under normal operating conditions, we can calculate their heat generation by this formula. However, for three-phase solid state relays and three-phase AC voltage regulator modules, the load currents on each of their phases should be added up as the actual load current and substituted into the above formula.
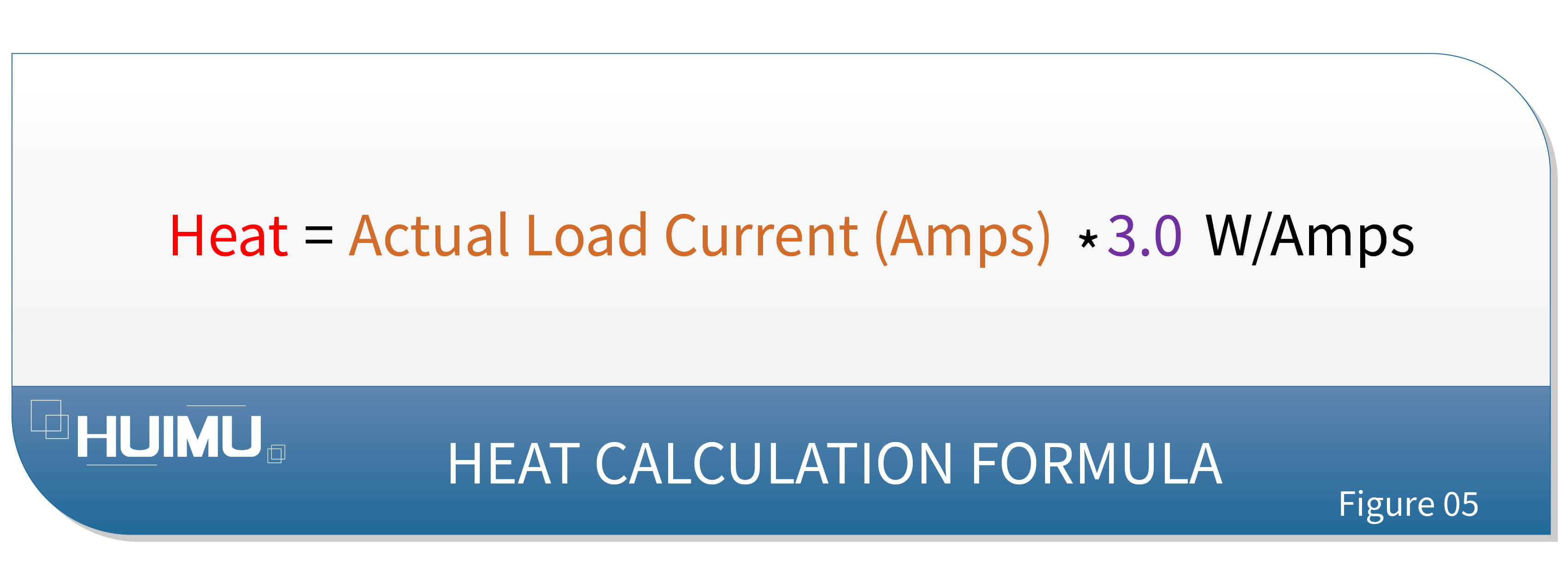
◆ Heat = Actual Load Current (Amps) * 3.0 W/Amps
This formula is suitable for single phase fully-controlled bridge rectifier module.
§3. How to select Heat Sink and Radiator?
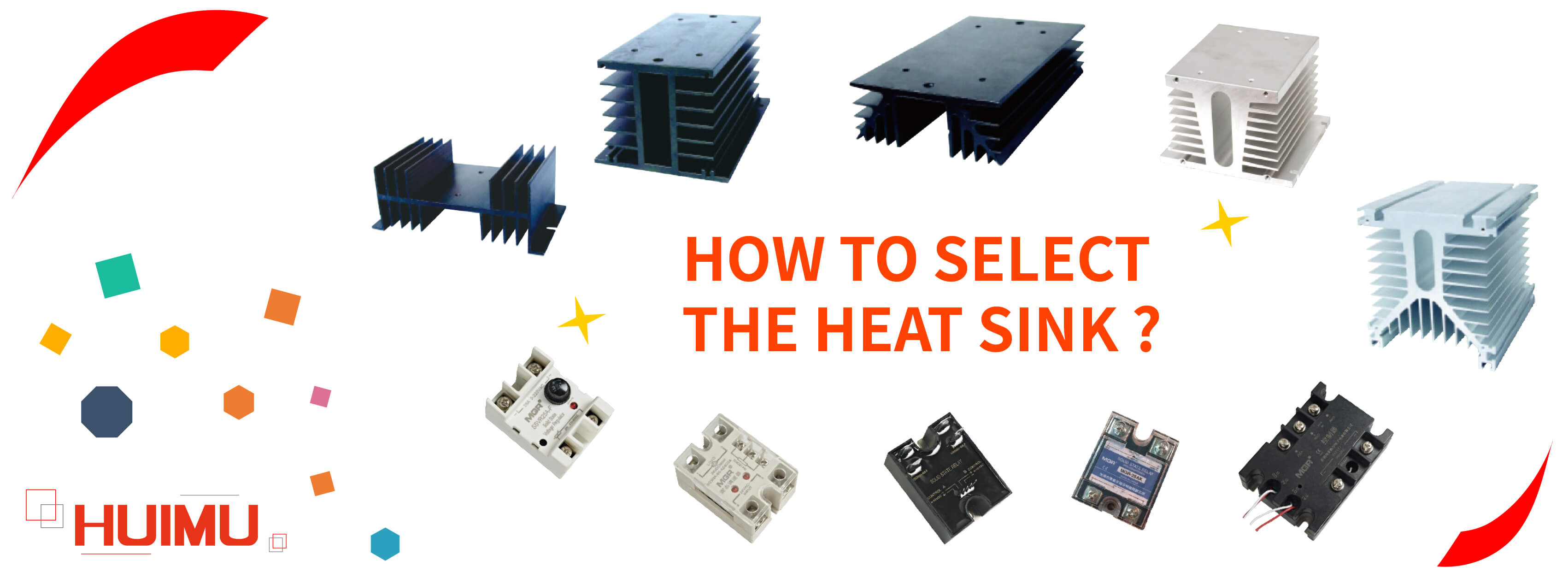
The heat dissipation devices for our products are divided into two categories, one is the heat sink for solid state relays, and the other is the radiator for solid state modules.
◆ Heat Sinks for Solid State Relays
MG-I, MG-W, MG-T, MG-L, MG-H, MG-F and MG-Y series are suitable for a variety of single phase solid state relays, single phase AC voltage regulator modules, R series solid state voltage regulators, industrial solid state relays and various three phase AC solid state relays.
◆ Radiators for Solid State Modules
E, K, Z, Y and G series are suitable for DC commutator modules, voltage regulator modules, rectifier modules, phase-shift trigger modules, thyristor modules, hybrid modules, welding machine modules. Since all these solid state modules consume a lot of power, they usually require an additional air-cooled fan.
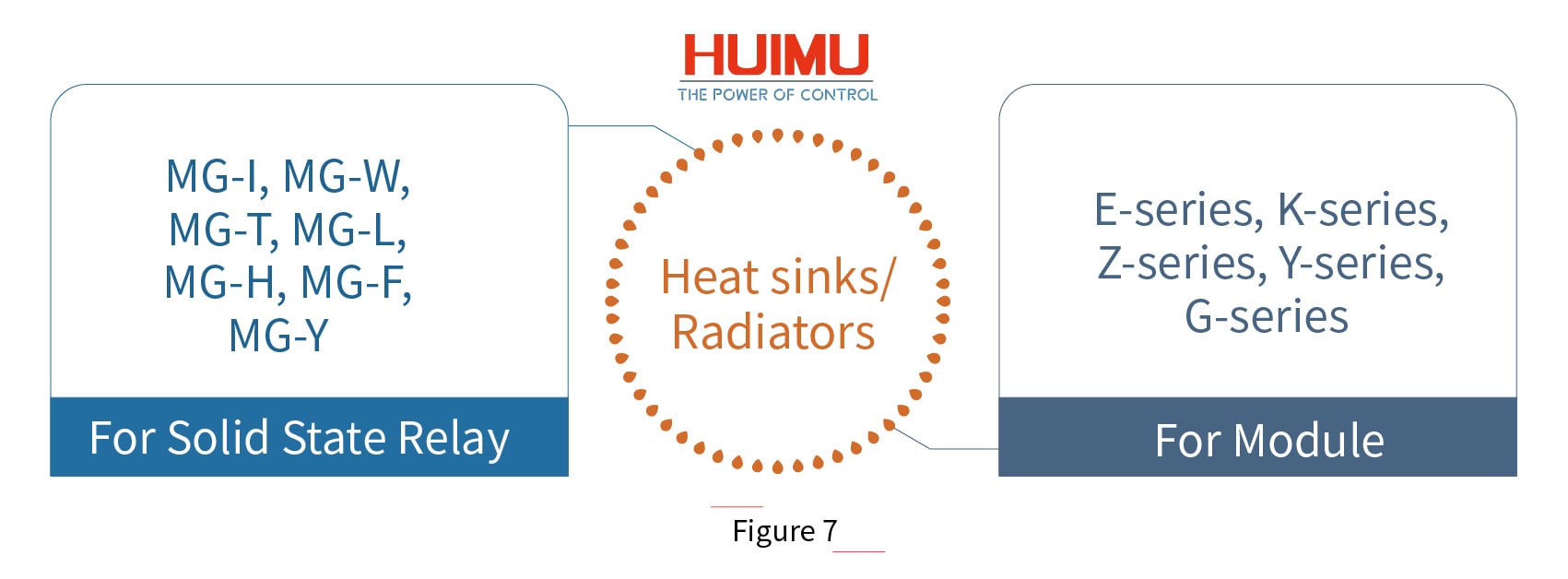
Below we provide some common solutions as a reference to further reduce the difficulty of selection.
● MGR-DT Series Full Isolation Single Phase AC Solid State Voltage Regulator Module
The heat of this module = Actual load current (Amps) * 1.5 W/Amps. You can select MG-L or MG-H series heat sink for it.
● MGR-DQZ Series Single Phase Full Isolation Fully-Controlled Solid State Bridge Rectifier Module
The heat of this module = Actual load current (Amps) * 3.0 W/Amps. You can select MG-L or MG-H series heat sink for it.
● MGR-STY Series Full Isolation Three Phase AC Solid State Voltage Regulator Module
The heat of this module = Actual load current (Amps) * 1.5 W/Amps. You can select MG-Y or MG-H series heat sink for it.
● SSR-3JK Series Three Phase Solid State Phase-Shift Trigger Module
This module is used with the random fire solid state relays manufactured by our company. The latest SSR-3JK series module already has an integrated synchronous transformer TB-3, so a voltage regulation system can be built with just three standard solid state relays and three MG-Y series heat sinks. However, if three industrial solid state relays are selected, a Y-series heat sink is recommended, with the addition of an air-cooled fan.
● SX-JK Series Three Phase Solid State Phase-Shift Trigger Module
If you already have a thyristor circuit, you can choose this series of modules without the need to purchase additional solid state relays. Due to the very low heat generation of this modules, there is usually no need to install a heat sink.
Get in touch with us now!
Please take a minute or two to complete this simple form to get reply in 24 hours, thank you!
*Please check the trash box of your mailbox, if you do not receive our email.